This conference call transcript was computer generated and almost certianly contains errors. This transcript is provided for information purposes only.EarningsCall, LLC makes no representation about the accuracy of the aforementioned transcript, and you are cautioned not to place undue reliance on the information provided by the transcript.
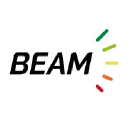
Beam Global
3/29/2023
Good day and welcome to the BEAM Global Year-end 2022 Financial Results and Corporate Update Conference Call. All participants will be in a listen-only mode. Should you need assistance, please signal a conference specialist by pressing star then zero. After today's presentation, there will be an opportunity to ask questions. To ask a question, you may press star then one on a touchtone phone. To withdraw your question, please press star then two. Please note this event is being recorded. I would now like to turn the conference over to Kathy McDormand, CFO. Please go ahead.
Great. Thank you very much. Good afternoon, and thank you for participating in BEAM Global's 2022 year-end conference call. We appreciate you joining us today to hear an update on our business. Joining me is Desmond Wheatley, President, CEO, and Chairman of BEAM. Desmond will be providing an update on recent activities at BEAM, and also following that will be a question and answer session. But first, I'd like to communicate to you that during this call, management will be making forward-looking statements, including statements that address BEAM's expectations for future performance or operational results. Forward-looking statements involve risks and other factors that may cause actual results to differ materially from those statements. For more information about these risks, please refer to the risk factors described in BEAM's most recently filed Form 10-K and other periodic reports filed with the SEC. of this call contains time-sensitive information that is accurate only as of today, March 29th, 2023. Except as required by law, BEAM disclaims any obligation to publicly update or revise any information to reflect events or circumstances that occur after this call. Next, I would like to provide an overview of our financial results for BEAM's fourth quarter and year ended December 31st, 2022. Revenues for the fourth fiscal quarter of 2022 set a new record for the company of $7.9 million, a 126% increase over $3.5 million reported in Q4 of 2021. Revenues for the year ended December 31, 2022, were a record $22 million, a 144% increase over $9 million reported in the same period of 2021. The increase in revenue was driven primarily by increased sales to federal, state, and local customers which has benefited from federal and state funding programs, as well as our GSA contract, which streamlines the contracting process. Revenues have also increased to enterprise customers for fleets and workplace charging, and we also recorded revenues of $5.2 million for our energy storage business from our recent acquisition of AllCell Technologies. Gross loss for the quarter ended December 31, 2022, with $0.7 million, or 9% of sales, compared to 0.3 million or 10% of sales in the same quarter of the prior year. Growth loss for the year ended December 31st, 2022 was 1.7 million or 8% of sales compared to 1 million or 11% of sales in the same period of the prior year. As a percentage of sales, the growth loss is improving primarily due to increased production levels, which resulted in favorable fixed overhead absorption and improved labor efficiency in spite of an increase in material costs for steel and other components due to supply chain shortages and other inflationary pressures, and a $0.8 million increase for non-cash intangible amortization related to purchased assets from the all-seller acquisition. Operating expenses were $7.1 million for the fourth quarter of 2022, compared to $1.7 million for the same period in the prior year. Operating expenses for the year ended December 31, 2022 were $18 million, compared to $5.6 million for the same period of the prior year. The 2022 increases were primarily due to a $5.5 million non-cash increase in the fair value of contingent consideration related to the all-sell acquisition, $3.4 million for the addition of all-sell expenses, $1.6 million for non-cash share-based compensation, $0.7 million for employee compensation, $0.6 million for legal and accounting expenses primarily related to the acquisition, and $0.5 million for sales and marketing costs to support our sales growth. The net loss was $7.8 million or $0.77 per share for the fourth quarter of 2022 compared to $2 million or $0.22 per share for the fourth quarter of 2021. The net loss for the full year 2022 was $19.7 million or $1.99 per share compared to $6.6 million or $0.74 per share for the same period of 2021. At December 31st, 2022, we had cash of $1.7 million compared to 21.9 million at December 31st, 2021. The cash decrease was primarily from increases in inventory and prepayments to vendors, secure battery cells production, as well as the net loss. Our working capital decreased from 24.6 million to 6.8 million from the December 31st, 2021 to December 31st, 2022. The decrease in working capital includes a 6.8 million increase in current liabilities for the change in fair value of non-cash continuing consideration related to the LFL acquisition. And with that, I will turn the phone over to Desmond to provide a business update. Desmond?
Thank you, Kathy. And thanks to all of you for dialing in to listen to this 22 earnings call. Looking forward to answering your questions after I make a few comments about the fantastic year that we just had. and what it means for our future. A couple of months ago, someone who I consider to be one of the best informed analysts in our industry asked me what would be for a normal company a very reasonable question. Should he expect 30% year-over-year growth from Beam Global? I laughed and I said, I bloody well hope not. We've been growing our revenues consistently for many years. The 9 million of revenue reported in 2021 was 45% higher than the 6 million we generated in 2020. And now we've just reported 22 million of revenue for 2022, or about 145% greater than the 9 million we reported in the prior year. At the beginning of the fourth quarter in 2022, we published a contracted backlog of not far off 300% of the full year revenues we were just reported for 2022. So said another way, starting back in 2020, 6 million in revenue, 9 million in 2021, 22 million in 2022, and about three times that much in reported firm contracted purchase orders as of the beginning of the fourth quarter of last year. The 60 plus million in backlog we reported in the fourth quarter by no means tells the full story of the 2022 growth in sales. Actually, our fantastic sales team secured over 76 million of purchase orders in 2022, which was a 548% year-over-year increase over 2021. And 2021 had already been 130% increase in new purchase orders over 2020. We sold over 800 EVR systems in 2022, which is more than all the EVR systems we've sold prior in the 10 years that we've been making the product. In each of 2022's four quarters, the value of the purchase orders we sold was more than 100% greater than the same quarter in the prior year. And in fact, in one of those quarters, we had an increase of 913% over the same period prior year. We had a 300% year-over-year increase in purchase orders of greater than $1 million per purchase order. Dollars, that is. We had an across-the-board reduction in the amount of time it took us to go from initial customer inquiry to a closed purchase order. So we're closing these deals faster, more urgency. In 2022, we made the largest, the second largest, and the third largest sales in our history. 367 EVR systems to the U.S. Army through our partner TechFlow, 140 systems to the Department of Veterans Affairs, and 71 systems to our largest municipal customer, New York City. This was the fourth or fifth order we've received from New York City, and by far the largest so far. Our previous largest purchase order, or rather our fourth largest, was a 52 system order from California's Office of Emergency Services. But then the fifth largest also came in 2022 as well, a 41 unit order from the Department of Homeland Security. There certainly was a lot of government purchasing activity at Beam Global last year. We received orders across all sectors of government, municipal, county, state, and federal. Interestingly, we received over $7 million worth of purchase orders from extensions of both our federal and California contracts. A word of explanation on this. We have a GSA or General Services Administration contract in place with the federal government, and we have a DGS or Department of General Services contract in place with the state of California. Now, normally when you have a federal contract, only federal entities can take advantage of it. And similarly, if you have a contract with the state of California, it's generally only available to government entities in California. But because of our EV charting infrastructure's products continue to operate during blackouts and brownouts, they're designated as disaster preparedness assets. And because of this, the federal government allows its contracting vehicle with Beam Global to be used by any government entity in the United States that cites emergency preparedness as a reason for acquiring our products. The state of California also allows other government entities to use the contract we renewed with them in 2022. Or actually, it was a new contract, but a return to another new contract with them. These perks, which arise from the fantastic value and unique nature of our product offerings, might not sound very impactful on first hearing, but when you realize that just about any government entity across the United States can now buy our products without going through any sort of competitive, time-consuming, and arduous processes, at a time when there's nothing but increasing urgency to deploy EV charging infrastructure, you can perhaps grasp why we've worked so hard to put these types of contracts into place. The proof of the pudding is that the federal and California contract extensions amounted for almost 10% of our sales in 2022. So yes, government contracts were a significant contributor to the fantastic growth we saw during the year, but actually only made up 65% of our total revenues. Only 35% of 2022 revenues came from non-government commercial customers. I would not say that we've seen a full return to pre-COVID revenue percentage mix between government and commercial. But the approximately 1200% year-over-year growth in commercial sales is certainly getting us back to close to where we were before COVID shut down almost all of our commercial business. Don't forget that even with that reduction in opportunities, we still managed to grow our revenues during those very trying periods. I've long been saying that while government tailwinds are important to our business, and indeed to the electrification of transportation in general, I believe that in the end, this will be a consumer-led revolution. The very rapid return of commercial orders that we saw in 2022 certainly does not dampen my enthusiasm for that conviction. And the fact that one or two of our recent commercial wins are with just the sort of customer that I believe might one day potentially become a sponsor of one of our driving on sunshine networks makes me even happier to see this return and continues my belief that we might at some point crack that elusive nut. I'm not aware of any other company in our industry, or in any industry for that matter, that can match our growth in sales. And yet one of two of our less cheerful followers delight in entertaining me with their doom and gloom predictions about our future. Oh, you've grown your sales for five years in a row and you've brought in some huge purchase orders from fantastic customers, says the unhappy soothsayer, but you'll probably never sell anything ever again. Well, and I have a crystal ball with which to combat such a fantastical and insupportable prediction. but I do have the closest thing that Beam Global has to one, our pipeline report, and a pretty damn accurate crystal ball it's turned out to have been. On January 1st, 2022, Beam Global's pipeline was valued at just over $80 million. We then brought in over $76 million of purchase orders in 2022. That is a fantastic pipeline to backlog conversion ratio by anybody's standards. In 40 years of business, I've never seen anything like it. Now, if you follow old doom and gloom's prediction, then we ought to have had something less than 5 million left remaining in the pipeline at the end of the year. In fact, our pipeline at December 31st, 2022 was approximately 120 million. That means that the sales team took an $80 million pipeline, converted 76 million of it into backlog, and then built it back up to over 120 million before the end of the year. And they're working more effectively and enthusiastically, in my opinion, than any time in our history. So much for doom and gloom. The fact is that by any reasonable metric, our sales are growing. And not only are they growing, but that growth is accelerating. That's true for the smaller one and two unit orders, which are actually becoming less and less common. And it's also true for the very much larger orders with price tags in the millions of dollars. I can see no end in sight to this trend. And in fact, anticipate it continually and accelerating further for the next couple of decades. Even our existing large contract vehicles are evolving to further streamline our ability to sell our products. For example, our Federal General Services Administration contract is now accompanied by a blanket purchase authority, or BPA, issued to us in 2022, which adds even more efficiency to the federal purchasing process. The state of California, with whom we've had a contract in place for many years, It issued us a new one in 2022, but with an expanded scope, adding more of our products, so it was already a fruitful contract for us. We make an infrastructure product, and as with any infrastructure solution, it's inevitable that there will be peaks and troughs in our selling cadence. But the very much larger order book that we now have will reduce choppiness in the revenue that we report, because as long as our sales continue to grow at these rates, and I see no end to that, Deliveries will be governed by our ability to continue to produce ever more and more product. We truly now have a supply challenge, not a demand challenge. So can we live up to the supply challenge? In 2021, we manufactured 119 EV arc systems. In 2022, we manufactured 244 EV arcs, 105% increase. In fact, in the fourth quarter of 2022, we produced 103 VR systems, 115% increase over the prior year, and more, in fact, than we produced in any full year prior to 2021. And it wasn't even very far of that full year's production. That's just in the fourth quarter. Just as our ability to sell our products is evolving and accelerating, so too is our ability to produce them. Beam Global's operational team has made excellent advances in adding efficiencies to our processes, and streamlining product throughput in our factory. Our engineering team has been in a near constant process of refining the design to make it easier to build while reducing costs and improving quality. These processes and engineering improvements have not stopped at the factory door. We can also see their impacts out in the field where we deploy. In 2020, it took two human beings to deploy a single EV arc. By 2021, we'd cut that to one person, And then in 2022, we approved upon that again. Through the addition of improved equipment, improved processes, and improved engineering, a single operator is now able to deploy two EVR systems, each of which can support as many as six EV chargers. There's a beautiful and very informative video on the EVR product section of our website, which shows you exactly how we do this. I encourage you to watch that video. Everyone who does is left with a greatly enhanced appreciation of the tremendous and unique value that Beam Global brings to the EV charging industry. There's simply no competitor who can come close to the speed and elegance with which our products provide infrastructure to support our customers' EV charging needs. We're deploying any quality brand EV charger, and often more than one of them, including popular brands like ChargePoint, Blink, Electrify America, and Enel, in less than the time it takes to write the scope of work for a contractor to start digging up your asphalt. Having produced two and a half times more EV arcs in 2022 than we did in 2021, we're now continuing to dramatically enhance our production capabilities because, of course, as I've already mentioned, we have about three times more units currently under contract than we produced in all of 2022, and our sales team continues to be highly active. More or less since our inception, our gross profits have been negatively impacted by fixed overhead allocations imposed as a result of our having facilities which are capable of producing far more product than we were actually selling. This has been especially true in the last few years since we moved to our 53,000 square foot facility just north of San Diego. Carrying that overhead burden would have been a very bad idea if we were in a flat or declining business. But as completely the opposite is the case, the fact that we have a great deal of excess capacity in our facility now seems like a very good idea. I always felt it was. That's why I did it. I'm now very glad to have the growth numbers to support my conviction. Analyzing the various constraints or bottlenecks which might impact our full capacity shows us that there are one or two choke points. The most obvious of those is that we have six final assembly workstations within which our teams pull together all the components and sub-assemblies of an EV arc into the completed product. Each of those workstations, when sufficiently staffed, is capable of producing an EV arc in a little less than a full shift. We're constantly improving upon that, and I believe that we can do quite a bit better. But using that cadence, we can do some simple arithmetic to ascertain what the maximum throughput could be in this facility. With all six workstations fully staffed and operating a single shift five days a week and discounting for all the holidays like Thanksgiving and Christmas, we produce about 1,560 units in a year. Multiplying that by our current ASP would generate just under $110 million in annual revenue. So that's one shift five days a week. Naturally, as we add shifts, we increase that throughput. Two shifts would be $220 million, and three shifts would get us about $330 million or 4,680 systems a year. And again, that's working five days a week and taking off all the holidays, which a normal business recognizes. In theory, if we work three shifts seven days a week, we could produce over 6,500 systems a year. But we don't live in a theoretical world. We have to be practical, which is why I drive my assumptions based upon approximately 4,500 units per year at full capacity. There are other steps we can take to accelerate our throughput, reduce costs, and increase our quality. Identifying certain sum assemblies and components which we manufacture in-house today but might tomorrow have produced by better equipped and more automated contract manufacturers is part of our plan for both reducing costs and increasing throughput without capital expenditure on our part. The whole team here at Beam Global believes that the EVR product is nearing a level of maturity in its development, which should enable us to take advantage of this sort of opportunity. External supply chain constraints can also have an impact on the amount of product we produce each year. And while we can never be entirely certain about what the future will bring in this respect, all of our observations at this point are trending towards reduced risk from supply chain interruptions. We regularly canvas our vendors to hear from them what they're seeing further upstream. We're successfully pushing them for cost reductions, better payments, and also assurance that we'll have access to the components and materials which we integrate into a final product. What we're hearing across the board is that supply chain risks are reducing and that costs, which we've seen consistently rising over the last few years, are plateauing and starting to trend down during the remainder of 2023. We're already starting to see some of those cost reductions in steel and transportation, for example. Of all the vital commodities and components that are essential to the successful completion of our business, or rather operation of our business, there's none more vital than cash. I look at cash in the same way that I look at steel or copper or battery cells or paint or electronic components or even labor. I want to get just the right amount, as much value and quality as I can, and I want to pay as little as I need to. One thing that should be abundantly clear after looking at our filings over the years that I've been running this great company is that I'm very disciplined with both cash and equity. Everyone on the team is. During our earlier years, we had to manage through difficult periods when there was little or no demand for the product and sometimes even less cash to support us as we created a company for the future that we felt so certain would come. Well, that future has come and we're going to be no less disciplined as we manage through these fantastic opportunities. Taking a look at our 12-31-2022 balance sheet, you'll see that we had cash of about 1.7 million, but we also had 4.5 million in AR at that time, and we always get paid. We showed a total current assets of 20 million made up of cash, accounts receivable, prepaid expenses, and crucially, inventory. These are all things that we convert back into cash in a generally short period of time. Our total current liabilities were 13 million, but that included almost 7 million in a contingent consideration for an earn-out payment as a result of the excellent performance of the battery company we acquired last month, non-cash. Performance-based earn-out payments are about as strong an indication as you can get the good value of a decision to make an acquisition. But to get an accurate picture of our financial health, it's best to look at the 20 million in current assets, discounted by the current liabilities, subtracting the contingent consideration. I'll give you the arithmetic for you. You take 20 million in cash, AR, prepaid expenses and inventory, all of which is pretty much the same as cash to us, and subtract $6 million of current liabilities derived by subtracting the $7 million contingent consideration from the $13 million, the answer you'll come up with is about $14 million of cash or stuff that we're going to turn into cash within the next few months. Quite a different picture. Now, let's look at what this $14 million in cash means to us. Total cash used in operations during 2022 was 18.1 million, as we've reported it. But that included 8.2 million in increased inventory, 600,000 in increased receivables, and about 800,000 in prepaid expenses and other assets, which, as I've already explained, essentially equate to cash for us. Again, doing the arithmetic for you, what that will show you is that the cash we actually burned, in other words, spent on stuff that will not turn back into cash again during the next few months, was about 9.5 million during all of 2022. That comes to less than 2.5 million a quarter. And remember that we closed an acquisition and integrated a formerly privately held company into the Beam Global family during that time. Taking that more or less 14 million in cash and stuff that we're going to turn into cash and dividing it by the 2.3 million, which is what we actually burned during 2022, you can see that we could operate for at least six more quarters without raising capital or doing anything else. And that's if our cash burn remained the same. This is also assuming that we get no gross margin contribution from our sales. But actually, we do get a contribution margin every time we sell an EVR. So the more than we sell, the less we should have to rely on our current assets to cover our overheads. More on that in a minute. Having excellent discipline where cash and equity is concerned is, in my opinion, very important to the long-term value creation of being global, for which I'm ultimately responsible. Nevertheless, it's possible to be penny-wise and pound-foolish. We're experiencing extraordinary growth, and I don't want to allow anything to get in the way of our executing on that growth. So while it's true that with disciplined cash management, we can continue to operate and grow for the foreseeable future, I've also taken steps to make sure that we have cash available to us to accelerate and lubricate our growth. Just last week, we announced a $100 million credit facility. to provide the kind of flexibility that we may need to prevent lack of cash being any kind of impediment to our rapid growth. We've spent a great deal of time researching debt and credit facilities and looking at other financing mechanisms which might be available to us. I can say with total confidence that I know of no other financing mechanism that could come close to competing with the facility we've closed with the London-based OCI group. As an investor myself, I know to be skeptical when reading the headlines of financings done by others. The devil is in the details, and there always seems to be some aspect of the deal which, as an investor, one wished did not exist. Well, I can tell you that the OCI $100 million credit facility is as simple and as clean as we have described it. What you see is what you get. There are no fees, no origination discounts, no underutilization penalties, no equity considerations, and no hidden gotchas anywhere in the deal. If and when we deem fit, we're able to bridge short-term cash deficiencies with this credit facility, and all we will pay is SOFR, or the secured overnight financing rate, plus 300 basis points. It's as simple as that. This was not an easy win. It took OCI and I, working in good faith, over four months to close this deal. As is often the case, arriving at a simple and clean conclusion takes longer than signing any old agreement earlier in the process. The reason that OCI is such an excellent fit for us stems from their extensive history of identifying where the real risks lie amongst the counterparties to the sort of sales transactions into which we will enter. Not by accident, Beam Global has targeted the highest quality and most credit worthy customers in the world. We have an impeccable history of delivering the products that our customers have ordered and an equally impeccable history of getting paid. Any typical funding institution would have based their underwriting decisions on Beam Global's profile and done whatever they could to leverage our need into an opportunity to take whatever they could get from us. OCI looked at our technology our history of delivering our technology, and the credit profiles of our customers. As Oliver Chapman, OCI's CEO, said in our press release last week, it's this beautiful combination which enables OCI to provide us with a meaningful credit facility at pricing and terms which would normally be reserved for blue chip entities. I stress again that we have a $100 million line of credit available to us at SOFR plus 300 basis points. There are no other hidden fees or mechanisms resulting from this facility. Please ask me questions during the Q&A session if this is not entirely clear to you. We'll continue to manage the cash and current assets on our balance sheet with the same high degree of discipline and care that we always have done, but we will not allow excessive prudence to slow our rate of growth. The OCI facility gives us the additional flexibility we need to free our operations teams to execute on the incredible opportunities that our sales teams are creating. Credit and discipline will always be important to us, but they alone will not make us the very profitable company that I believe we will become. Getting to profitability is, in many ways, the least mysterious aspect of our business. It's quite simple. Make enough money on enough products to cover all our overhead expenses, with some left over. The more that's left over, the better. The first step in that process is, of course, gross profitability, according to GAAP. But there's an essential step to get to that important milestone, and that is positive unit economics. If the variable cost associated with producing each of our products is less than the payment we receive from our customers who buy them, then we receive margin contribution from each of the units that leave our factory. I have reported often that our unit economics are positive. We are not a company that loses more when we sell more. We are the opposite. At a certain point, the margin contribution from the increasing volumes of product that we sell are sufficient to overcome the fixed overhead allocations with which we must also burden our costs of goods sold. When unit economics are positive, Increasing volume alone, when sufficient, will eventually lead to gross profitability. Reducing variable costs, such as the bill of materials and labor hours to produce the product, further improve gross profitability. We are doing all of these things. And the very positive result of these activities is that in the fourth quarter of 2022, our EV arc product line actually broke even at the gross margin line. A big contributor to the variable cost management for an EV arc is the fact that we're now producing our own batteries in our Chicago facilities. If we were still buying batteries from outside suppliers, we would have had to have absorbed all the cost increases which inflation and supply chain constraints have exerted on that industry, not to mention their margins. While we've also experienced cost increases, because we're making batteries ourselves, the impacts have been far less severe. Beam Global's approach to making our own batteries is, as far as I'm aware, unique in the industry, and it's playing an important role in our increasingly improved profitability. Our four-year gross margin for 2022 came in at about negative 7.5%, which is a 3.5% continued improvement over 2021 gross. Remember that we've improved our gross profit even in the face of the most inflationary environment that has existed in the United States for over 40 years and without increasing our prices. we face significant increasing costs of almost every material and component that we buy. This is true for all the products in our portfolio, whether they're energy storage or EV charging products. As I've already noted, we've experienced significant increases in the cost of components that go into our batteries, and yet they have still contributed to significant cost savings over the non-beam global auctions. It's also important to note that about 839,000 reported in our cost of goods sold was actually depreciation and amortization of intangible assets related to our acquisition last year, and not actually directly part of the variable costs associated with making our products. Removing these non-cash items from our cost of goods sold takes our gross loss from 7.5% to about 3.5%. A 3.5% pro forma gross loss, backing up the non-cash items, shows a pro forma gross profit improvement of over 7% when viewed against our 2021 results. Remember that this improvement has come a time, again, when we've seen nothing but cost increases across the board of materials and components we buy. Improvements in gross profitability have come as a result of increased volumes offsetting our fixed overhead as well as efficiency and engineering improvements. I track revenue per employee and revenue per laborer, and I'm seeing very distinct improvement in these metrics. I can sum this up by just saying that we are getting very much better at what we do. Another particularly graphic example of this is that we're producing about 10 times more kilowatt hours of batteries today than the company we acquired was in the month before it became part of Beam Global. We're in the same buildings and paying the same rent, and while we have increased headcount to accommodate our growth, we've not done so at anywhere near the same rate that we've increased revenues and productivity. Nowhere is this more true than when comparing revenues to overhead employees, where the growth has been even more pronounced, demonstrating the level of operating leverage that we have. Our actual operating expenses are much lower than we've reported when we take out about $8.4 million of non-cash items, such as the contingent consideration for the earn-out and some stock options and other non-cash items that are removed for comparison's sake. Removing these non-cash items, again, for comparison's sake, takes our operating expenses from 82% of revenue to 44% and also demonstrates almost 20% of improvement over 2021 results. So if you look at growth and net, be careful to understand that the acquisitions that we have done have added a lot of non-cash items, make the numbers look much worse than they actually are from an improving the business point of view. We need to continue to do a good job of analyzing these numbers because I think it's very unlikely that all cell technology will be the last acquisition that we make. On the contrary, I'm actively seeking opportunities to continue our inorganic growth while we knock it out of the park with organic growth. Buying this battery company and integrating it into Beam Global has been an excellent move for us on many levels. I've already discussed the significant savings that we've experienced as a result of not having to buy batteries from outside providers, but there are so many other positive aspects to this transaction. Part of the integration has been combining our marketing efforts and investing in more energy storage salespeople. We received over 8 million of energy storage orders during 2022, and our team did an excellent job of growing a new piece of our business while ramping up to supply all of our internal needs for batteries. Again, 10 times more kilowatt hours than when we bought them. The integration of the teams, which is never an easy thing after an acquisition, has gone very well. In fact, we have engineers from Chicago in our San Diego office this week. and the sharing of knowledge and experience and expertise across all the many areas of both our battery and EV charging infrastructure products has already contributed significantly to material improvements. We bought AllCell to reduce our costs, increase our revenues, defend our supply chain, and increase barrier entry for the competition. And we've seen quantifiable results in each of these areas over the last year. I will continue to look for other opportunities where I can acquire talent, technology, complementary offerings, and most especially for me at the moment, geographic expansion. One of the benefits of closing the OCI credit facility is that we now have a major European forward-thinking fund involved in our success. I've already stated how important I think the credit facility will be for us, but I also believe that having a strong and well-connected ally in Europe is going to be very helpful for us. I've visited Europe several times over the last couple of quarters, and I continue to feel enthusiastic about our opportunity to expand into the largest automotive market in the world, where I believe that our products may experience even more rapid growth and adoption than they are in the United States. I can tell you that I've already had discussions with OCI management, which go beyond the nuts and bolts of the credit facility. Europe's not the only international market which I believe holds prominent for us. I'm also looking at opportunities in another region, which I think could provide meaningful growth opportunities. And these activities are processes. They're not single events. They take time and a lot of work if they're to be done correctly. Some would have me rush into closing on the first opportunity which is presented to me. I will not do that. I will continue to seek out only opportunities and transactions which makes the best long-term sense for Beam Global, our shareholders, our customers, and our employees. The Beam team, has consistently shown that it can hit even the most aggressive goals it sets itself. I'm determined that international expansion will be another example of our succeeding. A part of doing future acquisitions right will mean balancing the use of cash versus equity when negotiating a deal. The AllSell transaction was a purely stock-based deal, and I believe it's worked out very well for Beam Global shareholders as well as for the sellers of AllSell. This is the way that these things are supposed to work. I'll endeavor to achieve win-wins with any transaction that I work through. There may be instances where it makes sense to use cash or equity or a combination of cash and equity. In either event, there will likely be some element of dilution. This is where our fantastic and historic discipline with equity issuance becomes even more of a trump card. The fact that we have about 10 times less shares outstanding than any public company that could be described as a peer means that we'll be able to grow our company using equity adding market cap, revenues, barrier to entry, geographic expansion, whatever else we might get from an expansion, while still having a far lower number of shares outstanding than our peers. If you're afraid of dilution, don't be. My job is not to maintain or increase your percentage holdings in Green Global. That's your job. My job is to increase the value of the shares that you hold. And if I and the board and all the other experts in our sphere agree that issuing equity to accelerate the growth of the company will increase shareholder value, then you can bet that I'll do it. We're entering a period of extraordinary growth in the industries which we target. The electrification of transportation and energy storage are just at the very beginnings of what will be, in my opinion, decades of growth. Just look at all the fantastic new electric vehicles which are hitting the market. Just look at all the regulations and investments made by governments around the world. Just look at the ever-increasing numbers of alarming reports from bodies like the UN and others, which those governments are using to inform their investments and regulations. Think of all the robots, drones, submersibles, micromobility, and other devices which will need safe and energy-dense solutions like those which we now produce. Just think of the fact that all of Beam Global's success today has been derived from one single market. Europe, the Middle East, and the rest of the world can benefit as well, if not better, from our products than the United States. The opportunities ahead of us are breathtaking. We will get better and better at producing and delivering our current products. We will introduce our future products like our EV standard and our UAV arc and all of the continued innovations I expect from our battery experts to markets which are hungry for innovative problem solving solutions like ours. We will continue to improve our profitability just as we have done even through this inflationary period. This is not the time to be timid about growth. This is not the time to stop investing in our future. We've demonstrated that we can take very little and turn it into a great deal. We've demonstrated that from tiny beginnings, we can create a meaningful platform. Now that we're standing on that platform, just imagine where we'll take it next. I'm thrilled and proud of what we've done so far, but I know that we're only just getting started. Now, it would be rude of me not to say hello to the shorters. This would be a great time for you to listen up. because I'm going to summarize. We have fantastic mass-producible, patented products addressing a massive and paradigm-shifting global infrastructure build-out. We have a made-in-America product at a time when state and federal investment is bigger than it's ever been, and it's being directed more than ever at American products. We have triple-digit growth in sales and triple-digit growth in production. We're improving our profitability against a tide of inflation, And that's a tide that will turn. We have plenty of room to grow and aggressive plans to expand in both the United States and internationally. We have no debt. We have great discipline where cash and equity is concerned and access to $100 million of cheap, non-dilutive and rapidly available credit. We are executing on every front and we have no indication that any of this is going to slow down at all. Quite the opposite. It's an absolutely brilliant time to be Beam Global. And now I look forward to answering your questions.
Thank you. We will now begin the question and answer session. To ask a question, you may press star then one on your touchtone phone. If you're using a speakerphone, please pick up your handset before pressing the keys. If at any time your question has been addressed and you would like to withdraw your question, please press star, then two. At this time, we will pause momentarily to assemble our roster. Our first question comes from Christopher Souther with B Riley. Please go ahead.
Hey, thanks for taking my question. Hey, how's it going? Maybe just starting out on kind of the revenue visibility and the backlog. I think you mentioned about 60 million. Can you talk through The cadence of backlog delivery here, is it really just how quick you can make them, or are there any multi-year type orders in there? I know some of the programs are multi-year. I just wanted to get a sense of some of the backlog is multi-year. You know, historically, it was, you know, backlog was maybe, you know, representative of what you were going to do in that quarter or so. And I just wanted to get a sense, do you think you're starting to become, you know, really a backlog company, or if it's really just, you know, ramping up and returning to that, you know, one or two quarter visibility based on the backlog?
That's a great question. And frankly, I'm remiss in not addressing that in my remarks. All of the contracted backlog that we have announced our customers want as soon as we can get it to it. So there are no multi-year contracts in here. When the Army orders from us, they're not saying, and it's okay, we can take this over the next five years or something like that. Quite the opposite. So all of the backlog we have announced our customers want immediately is And that's why I said in my comments that we really are now more supply opportunities and demand opportunities. The demand is clearly there. We've just got to catch up with it. And, again, that's helpful in terms of the previously choppy nature in our revenue. It won't be like that now. It's just going to be build more and more and more and more. And as fast as we can turn them out, we'll get them to our customers.
Got it. No, that's great to hear. And maybe just, you know, comments on supply chain as well as kind of the margin front. We appreciate all the color on the puts and takes, you know, from 2021 to 2022. But can you give us a sense or remind us what the component cost inflation headwind was for the year and, you know, for which we, you know, had to offset in order to get that 7% year-over-year improvement? I'm trying to get a sense of where your incremental margins are looking with, you know, as we scale and And maybe what else you're seeing as far as kind of the component cost moderation improvements and, you know, what we can do to, you know, improve the supply chain, you know, in best order, I guess.
Yeah. So, the last time I did a BOM to BOM comparison, a bill of materials to bill of materials comparison, same product. I can tell you that I was able to, and I didn't do a highly detailed dive, but even doing a not very detailed dive, I was able to identify 27% increase in costs of components and materials that we are buying. And again, I'm sure I would have found more if I'd have gone into the hundreds of smaller items that are on the BOM. 27% increase in costs during the last couple of years. At the same time, you are right to point out that we have improved our gross profitability by about 7% net of non-cash items over the last year. And I forget what it was, but it was another 3% or 4% or 5% the year before that, too. So you could say, putting all of this together, 27% increase in bond costs and yet an improvement of gross profitability of somewhere over 10% at the same time. You don't print money. It's got to come from somewhere. If we have to spend more to make the product and yet our gross profitability is improving, all that can tell you is that you need to combine those two things together to get a true picture of what we've done. And it comes to well over 30% improvement in gross profitability just over the last couple of years. Look, I don't like having a negative gross profit. I spend every waking hour working on this. So does the whole team here. And they've done a brilliant job of it, clearly, to extract these types of improvements during such an inflationary period and without increasing our prices. But the trend is very much with us. And everything we're hearing from our vendors, I just, for example, just had our battery cell vendor in here the other day from Korea. And he told me that we will see significant cost reductions in battery cells heading into the second half of this year. Battery cells are the single largest cost contributor to the product. Steel costs coming down. Transportation costs very much down from where they were just a year ago today. And all sorts of other opportunities for us to save money. we will become very profitable, the growth profitable profit line. And at the bottom line, if I didn't believe that, I wouldn't be doing this. And I've had plenty of experience with it. But again, the numbers support it. We are trending towards improved profitability, even at gap, certainly from the unit economics, even better. And I think the important thing to take out of that call is that our EVR product, which is the product that derives most of the revenue, broke even in the fourth quarter. GAP broke even in the fourth quarter. We don't segment our business or anything else like that. We have seven or eight different products that we make between batteries and EV charging solutions. But naturally, we look at how we're doing with each of them. And in this case, we know that we broke even according to GAP on the EV arc product in the fourth quarter. We do not intend to move backwards from that moving forward.
All right. I appreciate all that, Colin. I'll hop in the queue. Thanks.
Thank you, Chris.
The next question comes from Tate Sullivan with Maxim Group. Please go ahead.
Thank you. Thank you, Desmond. You mentioned growing the production of battery packs by 10 times since about March of last year. Are a lot of those battery packs going to your EV arc units, or can you bifurcate it a little bit, please?
No, they definitely are. I mean, the team over there has done a fantastic job. I'm so proud of them and so glad that they're part of the Beam Global family now. They really have completely upped their game from where they were when we acquired them. And, yes, they are now supplying all of our internal battery requirements. And the savings that we have received as a result of that are really very, very meaningful. I mean, it's a huge amount of money, actually. The beautiful thing about this acquisition is I'm confident that we will end up paying for the company just in gross margin recapture, never mind all the other benefits we're getting from it. So yes, a huge amount of what they produce came to us for internal use. But at the same time, we can't lose sight of the fact that they sold over $8 million of battery solutions to others. Those are going into drones and robots and submersibles. And I got to tell you, that's a side of the business I am very excited by. I don't want them just producing batteries for us. I want been global growing into all these other spaces. We have a drone recharging product. We have EV recharging products. I'm very, very strongly of the belief that there will be a tremendous increase in the use of robots of all sorts, whether they're airborne, submersible, terrestrial, or just bringing you a beer from your fridge in the future. I think we're going to see an awful lot of that. All of those devices are going to require energy-dense, safe, and well-packaged battery solutions. And that is what we are better, I believe, than anybody else at. So it's been a tremendous effort on their part. And we're going to have to expand. We have a 20,000 square foot facility in Chicago. We know we can't stay there because we need to expand. I fully intend to expand our EV charging product manufacturing into the Midwest and expand the battery manufacturing facility into the same location. some point in the future. And I also intend to expand battery manufacturing into Southern California so that we're making the batteries for the EV charging products that we make here right here as opposed to shipping them from Chicago. Not in any way dilutive to what Chicago is doing, accretive to what Chicago is doing. And the good news is that in the case of both of those expansions, I am led to believe that we will receive a great deal of help from the local governments in those areas. And of course, when I say help, I mean money. Most of it non-dilutive, well, all of it non-dilutive, and certainly most of it we probably won't even come with a repayment term. We grant money. So lots of great opportunity there.
Great. And then just on the GSA contracts you mentioned, just clearing up, you mentioned extensions to contracts with the customers through the GSA contracts, or did you extend the actual GSA contract structure? And how long does the current GSA structure last for contracts, please?
Yeah, so to be clear, what I mean when I talk about both the GSA and the California contracts is that, again, although those are normally restricted to only either federal in the case of GSA or California in the case of the California contract, both of those entities have made those contracts available in the case of the federal government to government entities who cite a disaster preparedness aspect for their purchasing decision. And, of course, that's one of the great strengths and one of the big decision factors for Army, Marine Corps, New York City, and so many others to buy our products, including a lot of corporations, by the way. They want to make sure they can still charge vehicles when there are blackouts and brownouts, which are happening more often today than any time in our history. Our products are a hedge against that sort of thing, and as such are viewed as a disaster preparedness solution. And quite a lot of buying decisions, buying our products, come from that alone, frankly. Never mind that we're much faster, lower focal cost of ownership, and cleaner and greener and everything else like that. A big part of the buying decision for many of our customers, government and corporates, comes from the fact that they know that we'll keep charting their vehicles during blackouts and brownouts. So the feds have extended their contract vehicle to anyone who has that requirement. And then California has just offered reciprocity to any other government entity across the nation that just wants to piggyback on their contract, which is fantastic. Of course, they want to support us, but they also have a mission to support the electrification of transportation. And what this means now is that other governmental entities who don't have the resources or the time or the inclination to put together an extensive and expensive and time-consuming and, frankly, risky bidding process, they don't need to. Some small town or state or other that doesn't want to go through the competitive process does not need to. They can perfectly legally buy off the California contract or off the federal contract. in the event that they have a disaster preparedness angle. And, I mean, some of them are pretty big. Dallas County, I think, was one of them we announced recently. They bought from us, but they bought through the federal GSA contract. So, you know, yeah, Dallas County is not exactly a tiny little backwater somewhere, and yet they use the GSA contract because they know it's been well negotiated, they know it's safe, and it saves them a huge amount of work. And, frankly, taxpayers' dollars going through that whole process of the of the competitive and very time-consuming process. There's a lot of urgency to get EV charting infrastructure right now. Urgency is our friend at Beam Global because we're so much faster doing it in less than an hour what others take a couple of years often to do. And so if they can avoid going through a lengthy RFP and contracting process and just jump straight on the GSA contract, they're going to do that. And that's very helpful for us.
Great. Thank you, Devlin. Thank you.
The next question comes from Craig Irvin with Roth MKM. Please go ahead.
Good evening. Hey, thank you for taking my question. So most of what I would have asked has already been covered, but there's a really interesting angle to your story that you didn't cover in your prepared remarks, the carbon credit angle, right? Over the next number of years, you're going to start generating quite a few carbon credits and there's an opportunity there to maybe monetize that. Can you maybe share with us where you are in the process of evaluating this, how this could potentially come together for you? What should we be looking for, or is this not really a short-term priority?
Well, I think it's fantastic that you've even identified it, and of course you're absolutely right. The simple fact of the matter is the cost of carbon, particularly in Europe, by the way, has accelerated dramatically. I think just two years ago it was about $21 for a ton, and it's now over $100 for a ton. An EV arc, which is the mainstay product that we produce, generates or removes over 12 metric tons of carbon per annum in its operations. That's a single EV arc. So if you think of just – if you look at our backlog today, multiply that by 12 metric tons. Now, of course, most of – well, in fact, all of the EV arcs that we produce today are owned by others, and we've enjoyed that business model so far. But I've made no secret of the fact that at some point in the future, it's not unlikely that we'll own a network of these things ourselves, either through a sponsorship model or some other business model. And in those instances, all of those carbon benefits will inure either to us or to whoever we want them to. And there is a very significant monetary aspect to this, which has not been realized by us to date, not been reported by us today. And certainly, I do not think before you brought it up, being recognized at all by the markets. But, yes, it's very real, and it's that kind of recurring revenue that I know that people are so eager to see us producing.
Excellent. Then as a follow-up, you haven't really mentioned or focused on sponsored deployments in quite a while, at least in your public communications space. Are there any developments there that you might be able to share with us, or is this something that, you know, we still should consider maybe on the back burner while you really focus on serving demand that's already pretty intense right now?
Thank you for recognizing the demand is very intense at the moment. There's no doubt about that. People are unragged around here, but I'll tell you what, there's a brilliant energy here. There's a fantastic buzz both here and in Chicago. Everybody feels like they're on a winning team because they are. Look, the fact is I've been talking about the sponsorship network for some time. I am still confident that we will get it done. You know, I've made a lot of commitments over the years since I've been running this company. And with the help of the fantastic people that I have around me, I've kept all of them, all of them. Except for this sponsorship thing. It's the one thing, the one nut that we haven't been able to crack yet. I do not want to describe it as being on the back burner because it certainly isn't for me, nor is it for the superlative group who we have working to help us sell that. And again, remember, they are working for nothing but performance-based pay. We're not paying them a retainer or anything. These guys are like the preeminent experts in the United States in selling sponsorship deals. If they think it's worth putting the work in for, you know, on the come, as it were, presumably they've got a good feeling for this thing. I can also tell you that I continue to talk to parties who could become sponsorship and have indeed shown an interest in doing so. It's just not closed yet. And I'm conscious of the fact that people are sick of hearing me saying that we'll get it done, and I'm not getting it done. Although, as I say, it's the only damn thing that I've committed to in the last 12 years that we have not done, again, with the help of the tremendous people around me.
So I will tell you, if you're asking me, Desmond Wheatley, what I think about this, that right now.
I still firmly believe we'll get it done. I just wish I could tell you exactly when, but I can't. But we're going to keep on it because it's such a beautiful model.
Well, I'm not surprised you're tenacious there. So good luck. We look forward to the progress. I'll hop back in the queue.
Thank you, Craig.
The next question comes from Noel Parks with Toohey Brothers Investment Research. Please go ahead.
Hi, Noel. Hi, good afternoon. Just had a couple things. I was wondering, you know, I think in the last three months, six months, and I was just wondering if any of these emerging technologies, you know, some requiring lower or alternatives to lithium. Have you seen any out there that you would consider worthy of investment in either, you know, minority or acquisition? I'm just thinking about your sort of longer-term storage portfolio.
Yeah, so there's a lot of things wrapped up in that question, Noel. First of all, we're an innovation company and we applaud anybody out there who's innovating, particularly when it comes to that intersection of clean energy and transportation, which is where we are focusing. That's obviously a pretty massive area to focus on. But nevertheless, that's what we're focusing on. So the first thing I'm going to tell you is that at the moment, we believe that there are many, many years. of lithium-based battery business growth ahead of us many years, probably 10 years, in fact, before something like Solid State or whatever else like that comes along and really displaces that. And you don't have to take our word for it. You just look at the massive investment being made by all the sort of much larger entities out there who are concentrating on that. And so I think we're certainly going to continue to improve our expertise and bring the value that we do to making lithium particularly NMC cells, safer and more energy dense and longer lived than they are today, which is essentially what we do. And then beyond that, there are some other things to think about, too. Just charging and discharging a battery in general is going to create a thermal event. That's physics. It's not anything to do with brand or anything else like that. And so having great thermal management solutions, as we do, will be a differentiator for us no matter what technology comes out, frankly, because batteries like that Goldilocks zone and they're safer if they're in a Goldilocks zone. And that's one of the things we provide for them. To your question about whether or not we'd invest, I'm not so arrogant as to think that I should take money that people have invested in this company and reinvest it for them in that way to where we would be an outside investor. I'm going to concentrate all of my efforts on growing Beam Global. If I see a promising technology or a solution, or geographic growth or talent or any of the other things that I think will grow, beam global, then I will invest in it. Again, with the advice of my board and all the experts that I surround myself with. But I don't think you should anticipate us making a sort of a third-party outside investment in some other technology at the moment. We're too busy growing our own company to worry about growing anybody else's.
Sure. Fair enough.
I was wondering, the There will be a somewhat higher percentage of total revenues in 2023. Do you have any sense of that, any insight on that?
I mean, you know, we're bringing, this is one of these perfect marriages. These guys have great product, great technology, great expertise. We are definitely, though, enhancing their sort of ability to sell and expand. I mean, that's part of the reason that they allowed themselves to be acquired by us or enjoyed being acquired by us, frankly, because they were looking for ways to expand. So we're enhancing their selling. We're enhancing their market. I mean, I mean, hiring more salespeople. We're enhancing their marketing and we are making investments that we need to make in enhancing their ability to produce. I mean, you know, this is part of the reason our operating expenses have gone up this year. I know that that will raise some eyebrows, but this is, as I said in my closing comments, this is not a time to be churlish about investing in growth. On the contrary, we need to be really aggressive about it because we have such a good thing going. So they'll do a lot more, I believe, this year. But I'm not certain that the percentage of revenue will increase because, of course, the percentage of revenue on the EV charging infrastructure product side of the business is so dramatic.
Right, right. Actually, the minute you started laying it out, I was thinking that's right. The growth on the charging side is so likely to sort of swamp whatever trends you might have on storage, standalone storage. It totally makes sense. And I guess just the last thing, I just wonder if there's anything else as far as around IRA issues that it seems like a lot of parties are still waiting for, particularly from the IRS. Anything on the horizon with those that has crossed your radar screen during the quarter?
Yeah, so I will say this to the simple answer to your question, as I am certain that we will see benefits from not just NEVI, but from the other couple of billion dollars that federal government's committed to enhancing EV charting infrastructure, or to the 10 or so billion dollars that California's putting into it or to all the other spending that's going on. I mean, you know, there are specifics in NEVI, which I frankly think are going to be really hard to execute on. The idea of having 600 kilowatts of charging every 50 miles on the highway system in the United States is a fantasy. The electrical grid simply doesn't exist to do that. And actually, that would be a great opportunity for us, for example, for our solar tree product, not so much for the EV arc product, but for the solar tree products, I think there may be locations where there's 300 or 450 kilowatts, but not 600 kilowatts. And we might be able to fill that last 150 kilowatts for them in a really clever way without having to do all the infrastructure buildup. I don't see that as necessarily a this year thing for us, but I definitely think that that will happen as they recognize that some of the Some of the shortcomings in the plan, as it were, that needs to be filled by different and innovative solutions, just like ours. On the $2.5 billion that's going to be spent, a lot of it's going to go to disadvantaged communities. There's money set aside for tribal lands and all sorts of other things like that. I just don't know of a better solution than ours to do that. We've already demonstrated that deploying in disadvantaged communities through the Electrify America deal and also through several transit authorities. We're very good at that. We bring clean, green, driving on sunshine with no unit cost for the electricity to these environments where people don't have money. And a lot of that money is going to be channeled in that direction. So I think we will do very, very well out of those things. for us to get to 35% of revenues in a year where we had such huge government growth as well. You can see that we're often sort of people say, oh, you're all government. No, we aren't. 35% of our revenues came from commercial, and I think we're going to see that continuing to grow as well. And at the end of the day, I think commercial wins, just as it should.
Right, right. And I think you alluded to this in your remarks, and that's really in the context of sort of all things commercial, really, really hitting the brakes during COVID, right, and the after effects of that. It's kind of the rebound from that, I believe you referred to.
There wasn't too much workplace charging being installed when no one was going to offices anywhere in the country. And we really were impacted by that. But we're seeing it coming back with a vengeance.
Great.
Thanks a lot. Thank you, Noel.
The next question comes from Abhi Sinha with Northland. Please go ahead.
Hey, Desmond. Thanks for taking my question. Quickly, I wanted to ask, could you give us some sense of idea of how or what percentage of your revenue in 2022 or even in your backlog is coming from repeat customers?
That's a good question. Lots and lots and lots of it. So, I mean, obviously, New York is the most obvious one to mention there. So we got a $5.3 million purchase order from New York City. They've been buying from us since 2015, I think. And by the way, every time they give us an order, it's bigger than the last one. We love working with them, and we think they're doing really great work over there. When you look at things like the Army order, you could say in a way the Army order is a repeat order because it came through the GSA contract, so it's all coming through the same contracting vehicle. I don't think that's fair. We have contracts like the GSA contract and the California contract, and we have to report a lot of concentration because we've got these orders coming in through the same contract vehicle. But in fact, to say that an order from the Army is the same as an order from Department of Homeland Security or the U.S.
Marine Corps, although they may come through the same contract.
Especially amongst those people who bought one or two of our products in the early days to sort of test it, back in the days when we used to have to prove ourselves, I think we're way beyond that now. But we've had great success. I'm sorry I can't give you an exact percentage on that because it's so hard to muddle out what's GSA, what's California, and everything else. But I think we love repeat orders, especially when they're bigger than the one that we got before from that customer, and I think we've seen a lot of that.
Sure. No, I'm just trying to understand, like, with that sense of idea, then – you know, what's stopping you from basically giving us some kind of guidance in terms of revenue number or unit sales number that will help the street out there?
Well, I'll tell you why I'm not giving guidance, because I think it would be foolish of me to do that. Imagine if, you know, in the beginning of 2022, Ida said, well, we're going to double our revenues and we're going to end the year with 300% of that year's in contracted backlog. I mean, you know, it's just there are too many moving parts that we don't control. Remember that we are in an industry which is a brand new space, brand new technology, brand new. There is no historical playbook. I can't look back at any sort of ratios or anything else like that. I certainly would never have suggested that we would convert 80% of our pipeline into backlog. I would never suggest that because, like I said, I've never seen that in 40 years of business. So the fact is that none of us have enough information about what the future will hold to make accurate forecasts. What I am absolutely convinced of is that we are going to continue to see very dramatic and accelerating growth. And again, I'm convinced of that because the small amount of data that I do have to look at, things like the pipeline returning to over $100 million after we took $76 million out of an $80 million pipeline, if you think about what that actually means, that's pretty dramatic. And it always indicating, telling us that we're just going to sell more and more and more. And I'm very, very confident in the fantastic team that we've got here. And as I said, the fact that we've got underutilized space here still, we will be able to grow into that. But I'm not going to give guidance.
Sure. No, fair enough. Last one I have is, and I'm just trying my luck here. So could you help us and, you know, get some idea on like, so what would be the, dollar revenue number or maybe unit sales numbers that kind of somewhat threshold that you have in mind to get a breakeven gross margin here?
And would that be in 2023 that we can think of?
Yes, I've asked and answered. We were breakeven gross profit on EVR products in the fourth quarter.
Got it. Sure. Thank you very much.
Thank you.
The next question comes from James McCulloch, a private investor. Please go ahead.
Hello, Jasmine. Good to talk to you again. Just a general comment in terms of the market opportunity. It seems like you're looking at a billion-plus easy market opportunity, and the challenge for Beam is going to try and get to a critical mass to take advantage of that. So Two conference calls ago, one of your, I think, esteemed older private investors made a recommendation to go out and secure a significant credit line or financing for growth. So congratulations on executing that. So obviously, that was a critical piece. I had two questions. The first one was around the current product line. One was, how strong is your patent protection for the EV charging systems that are not connected to the grid? So how strong do you feel that patent protection is, and when do those patents expire? And then the second question was regarding competition. Are there any current competitors of a larger scale that actually are offering competing systems, again, non-grid connected systems? I've got a follow-up question.
Yeah, so thank you for the comment about the credit facility. You're absolutely right about that. I mean, clearly it's magnificent for us to have access to that kind of cash. And again, very inexpensive, non-dilutive, and with no fees or gotchas or anything else like that. It was, again, a hard one to grind out, but I'm delighted. I'm really thrilled with the partner that we have as well. You should definitely take a look at them. Third largest or third fastest growing company in Europe and first largest in the fastest in the United Kingdom, very well respected, multi-billion dollar deal type of organization. To your questions, the patent portfolio that we have is fundamental to our product. And what I mean by that is there are several patents rolled up in, for example, the EVR product, and all of them are fundamental to its operation. In other words, you can't get close to an EVR and not be infringing on our patents. And that was really deliberate on our part. We are about halfway through the life of the earliest of those. And we will, of course, pay attention to that and endeavor to make such improvements and changes as we can to the product in the future to allow us to roll new patents into it, as it seems like that's the right idea to do it. And we will rigorously defend our patent portfolio. I mean, the great news is we don't need money to do that. This is America. There are plenty of people out there that would happily take that on spec because our parents are well-written and they'll fight on our behalf for a piece of the proceeds, of course. Again, it's America. No one does anything for free. But I think we're well-defended where that's concerned and certainly for the foreseeable future. As far as competitors are concerned, you asked me if there's any sort of, I think you said well-heeled or at least, you know, larger capable competitors. I don't know of any competitor that has anything like what we have rapidly deployed, transportable. We've seen no hint of it, except that there are a couple of smaller companies out there who are making things that might look a bit like it, but they can't really compete with it. For example, and here I'll pre-sell the negative, we actually lost a contract last year to a company that takes 20-foot shipping containers and fixes solar panels onto the roof of those containers, puts some batteries inside of them, and then attaches EV charging to the outside of the container. Now, they can compete with us almost on speed to deploy. They're still not as fast as we are. They're certainly nowhere near as elegant as we are from a deployment point of view because they still have to kind of bolt it together. Their units don't fold out hydraulically like ours do when they hit site. And, again, I encourage you to watch the video on our product section, EBR product, to show you exactly how this is done, and it's really elegant. But there are several things wrong with container-based solutions. First of all, a shipping container does not fit into a standard legal-sized parking space. which measures 9 foot by 18 feet in the United States, you are going to stick two feet out into the drive aisle. In many instances, that is illegal because drive aisles are often also fire lanes. A shipping container will render the parking space unusable, unlike our product, which allows you to park on it. A shipping container will prevent you from parking in that space, and most jurisdictions that we care about have a minimum requirement for the number of parking spaces available. which are required for the use on the property. Taking away even just one of those spaces will knock the property out of compliance. You might get away with that for six weeks or six months, but you're not going to build a business out of it. And then from an energy density point of view, the shipping containers can't compete with us because they don't have our patented tracking solution following the sun as it moves across the sky and generating a measured 25% more electricity, which just means more miles into the electric vehicle. And then finally, dare I say it, most people do not want 20-foot shipping containers parked in front of their buildings, even if they are providing EV charging. And I'll tell you this, the entity for whom we lost that contract that ended up selecting the shipping container solution because it was less expensive than ours, and we don't even know if they're going to be able to deliver it, But the entity that did that, I can tell you that the actual site recipients, the host sites there, are bitterly disappointed that they're not getting what they now refer to as a beam. We call it an EV arc, but most of our customers just refer to it as a beam. And those recipients, not the people who close the contract, who so often are not the ones that actually use the product, but the recipients of the devices are bitterly disappointed that they ended up with an old 20-foot shipping container instead of a beautiful device.
well engineered product like ours okay and you mentioned you're halfway through the patent life and the first ones to roll off how many more years left on that another 10 or so okay so you've got 10 all right so the second question on the current cost and then I just want to get into market expansion in Europe and you mentioned you made a brief mention on the Midwest as well Freight cost is a percent of your sales of your finished products, say, for example, to the East Coast for both the shipping the finished product as well as bringing in raw materials into San Diego. What percent of the total product cost ballpark is your freight, and is it prohibited from a cost standpoint and logistics standpoint to be shipping a significant amount of product to the East Coast, for example? Well, of course, we have shipped these to us because we've had to.
We haven't had a choice. I think one of the ways we cure for that is, as I said, we do intend to expand into somewhere in the middle of the country. It makes a lot of sense for us to be there from a whole host of reasons, less expensive to do business. hospitality in this kind of skill sets that we choose, I think we're already starting to see a decline there and there'll be a lot of people available for us. So we'll save money that way. The percentage costs are so varied depending on where we're going and whether or not we self-perform or how we move. So just to be clear, sometimes we deliver ourselves using our own equipment, sometimes we use third-party carriers, and sometimes our customers do the delivery. And so we don't even do that. So they're very varied. In no instance are they prohibitively enough to prevent us selling and deploying the product, but we would certainly love to bring these costs down. And what I'll tell you is we have seen as much as a 5x decrease in costs. For example, to ship a container across the Pacific Ocean from where the battery cells that we buy still come, 5x reduction in costs, dramatic reduction in costs to move a truck across the United States, and even more than the cost reduction where last year for love nor money could we even get them to show up this time last year because they were so busy And now they're calling us looking for loads. And when trucking companies are calling you looking for loads, two things going on. First of all, you're moving into a recession at some point or something that looks like one. And the second thing is you pay a lot less. Now, where recession is concerned, I want to be actually very clear about something. We have absolutely no top line risk to right now from recession. None. But I think it might go the other way. I think we might do even more because infrastructure buildups and so on will be so important. But at the same time, I do anticipate a continued and even more dramatic reduction in our costs moving forward as a result of reduced demand and slowing of the inflationary environment and all sorts of other things like that. So one never wants these things to happen, but I think we're about as good a position as we could possibly be if something like that does come down the pipe.
That's good to hear. And then the last question on the current product was on pricing. You mentioned that you're pretty proud that you would not increase pricing and yet been able to reduce the gross margin operating loss. Are there any restrictions in the GSA and other contracts that actually prevent you from raising prices, or is it more market forces? And if there are restrictions, when do those roll off in terms of, is there a provision in the contract that allows you to raise price based on either raw material or time?
So let me be clear. I am proud of my fantastic team for the fact that they have been able to reduce our costs. I'm not proud of myself for not increasing my prices. I'm neither proud nor anything else where that's concerned. This has been an entirely pragmatic decision on our part based on our belief that at the moment, growing the business, increasing volumes, getting more market share, getting more footprint out there is absolutely crucial to our long-term growth and profitability. And that raising prices would be just adding an additional barrier. And I'll tell you personally, I don't like raising prices to solve profitability problems. That's not where the work is. Anybody can do that. The work is in reducing costs. And that's what we are absolutely focused on. And we believe that even where we are, With the current pricing, without increasing our pricing right now, we believe that we can get to a 50% growth profit in the future. And that's the job, is to get to that, not just raise the prices because it looks good on a spreadsheet. It's not to do with restrictions on GSA contracts or anything else like that, although, of course, there are contracted or negotiated prices in those things. So we would be able to increase them whenever we renegotiate those contracts or if there's some extraordinary event that we're able to demonstrate to them. But that's not the real interest here. The real interest is in growing this business and in continuing to do what we've done over the last couple of years, which is have these triple-digit growths. Believe me, we will get the profitability out of it. Anybody that mass-produces a product does.
Clearly. I just – given the environment that we're in right now and the cost increases that everybody has incurred, some of them permanent – the opportunity for a price adjustment to reflect some of those increased costs. Everyone's accepting it. Sounds like you've got a product that's in high demand, and price is not the main determining factor in the purchase decision for this. So, just a thought. The last second part of this was just on the expansion plans, particularly as far as both Europe and within the United States. If you could maybe elaborate a little bit further as to which is, is there one that's more of a top priority. And then on the European, any thoughts as far as Europe? Does the EU have similar GSA national or not even national, but contracts within all the member states? Or are the incentive programs negotiated with the individual countries within the EU? And have you Given any thought at all in terms of strategy, whether it's Greenfield, partner joint venture with an established player in Europe.
Okay, so from an expansion point of view, I'd say you could break it down like this. From the beam team point of view, U.S. expansion is the thing that they're concentrating on. From Desmond Wheatley's point of view, European expansion is the thing that's most important to me right now. And we do kind of, you know, I will be the sharp end of the spear where that European expansion is concerned, not just because I'm from there, but just because it's appropriate that I would do that. It's a strategic type of negotiation, whereas the U.S. expansion will be something that's more operational and administrative. And, you know, we've got lots of really good talent on the team to do that sort of stuff. I don't think it's where my strengths would be best represented here. But negotiating either in an acquisition or some other means of expanding into that market, maybe that's where I think that my skills will be best represented. So to answer your question about whether we would consider a joint venture or something like that, not in Europe. I think in Europe we want to own it. We don't want to give up any of the equity in that space. But there are other parts of the world where a joint venture makes a lot of sense for us. Those are parts of the world where you just don't do well unless you've got a strong and powerful local partner. And so I think you should expect me to be very pragmatic about this. If I'm going into an environment where we think a strong and powerful local partner is good, then joint venture it is. If we're going into a place where rule of law governs and where we want to own all of the equity, then we're going to acquire or bootstrap. And I would say acquire would be my preference on that just because of speed to market. And then finally, on contracting in the European Union, certainly there are buckets of money available at EU level that are being transmitted through the local states. And then I think we're going to see a lot of local contracting within those states as well. But as you know, the government in Europe, governments and government in Europe, tend to be a bit more engaged in sort of infrastructure. There's less of that kind of laissez-faire thing that goes on in the U.S. where the markets are expected, public markets and commercial entities are expected to take care of these things, and a lot more centralized infrastructure planning, et cetera, in Europe, both at the national level and at the EU level. And I believe, and this is an informed belief, it's not just a guess, that our products are going to be very popular over there For all the reasons that they're populated in the United States, but perhaps even more so. It's actually harder, more environmentally impactful to start digging up the streets in a place like Paris than it is in a place like San Diego because of all the history and all the other stuff that goes on there. There's a much more tendency towards green energy in Europe than there is in the United States. And then energy security, particularly after Mr. Putin's behavior over the last couple of years, energy security is absolutely front and center for everybody over there. They're terrified that they're paying too much for the unit of energy. And, of course, there's zero unit cost of energy with our product. And they're also terrified about vulnerability where energy is concerned because they have seen over the last couple of years just how very vulnerable they are. And so there's just so many reasons why that's an exciting market for us. And that's why I tell you, from a personal point of view, that's where most of my focus is going to go. Okay. Thank you very much, Desmond. Congratulations. My pleasure. Thank you. I think that's it. We're a little over time here. For those of you who are still on, thank you for spending the time with us. Thank you for your support and for your excellent questions. The great thing for me is every time I do these, they're better than the last because we just keep knocking it out of the park. And I do not want you to anticipate there'll be any flow down in that because I don't think that's coming at all. As I said, it's a brilliant time to be being global right now. And there are plenty of challenges ahead, but they become less all the time. And those challenges are more to do with the tremendous new opportunities that we have than the sorts of things that we've had to overcome in the past. So thank you for being along for the ride. and I look forward to doing the next earnings call.
The conference has now concluded. Thank you for attending today's presentation. You may all now disconnect.