This conference call transcript was computer generated and almost certianly contains errors. This transcript is provided for information purposes only.EarningsCall, LLC makes no representation about the accuracy of the aforementioned transcript, and you are cautioned not to place undue reliance on the information provided by the transcript.
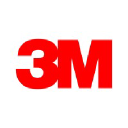
3M Company
10/26/2021
Ladies and gentlemen, thank you for standing by. Welcome to the 3M Third Quarter Earnings Conference Call. During the presentation, all participants will be in a listen-only mode. Afterwards, we will conduct a question-and-answer session. At that time, if you have a question, please press the 1 followed by the 4 on your telephone keypad. It is recommended that you use a landline phone if you're going to register for a question. As a reminder, this conference is being recorded Tuesday, October 26, 2021. I would now like to turn the call over to Bruce Germelan, Senior Vice President of Investor Relations at 3M.
Thank you and good morning, everyone, and welcome to our third quarter earnings conference call. With me today are Mike Roman, 3M's Chairman and Chief Executive Officer, and Monish Patolawalla, our Chief Financial and Transformation Officer. Mike and Monish will make some formal comments, and then we'll take your questions. Please note that today's earnings release and slide presentation accompanying this call are posted on our Best Relations website at 3M.com under the heading Quarterly Earnings. Please turn to slide two. As we have done throughout the year, I'd like to remind you to mark your calendars for our next earnings conference call, which will take place on Tuesday, January 25th, 2022. Please take a moment to read the forward-looking statement on slide three. During today's conference call, we'll make certain predictive statements that reflect our current views about 3M's future performance and financial results. These statements are based on certain assumptions and expectations of future events that are subject to risks and uncertainties. Item 1A of our most recent Form 10-K lists some of the most important risk factors that could cause actual results to differ from our predictions. Please note, throughout today's presentation, we'll be making references to certain non-GAAP financial measures. Reconciliations of the non-GAAP measures can be found in the attachments to today's press release. Please turn to slide four, and I'll now hand it off to Mike. Mike?
Thank you, Bruce. Good morning, everyone, and thank you for joining us. In a dynamic environment, our performance throughout 2021 has shown the skill of our people around the world, the resiliency of our business model, and the relevance of our technologies. In the third quarter and year to date, we have delivered broad-based organic growth across all business groups and geographic areas, along with good margins and strong cash flow. Q3 organic growth was over 6% as we drove innovation across our market-leading businesses, with margins of 20% and earnings of $2.45 per share. Geographically, growth in the quarter was led by the Americas, up 7%. with the United States up 6 percent. Growth in APAC was 6 percent, with China up 3 percent and Japan up 6 percent, while EMEA grew 4 percent. With respect to the macro environment, overall end market demand remains strong, though the semiconductor shortage continues to impact many markets, most visibly in electronics and automotive. As we navigate near-term uncertainty, we continue to invest in growth productivity, and sustainability, which I will discuss shortly. We are also actively managing disruptions in the global supply chain with a relentless focus on customer service. Looking at our performance through nine months, we have executed well and delivered 11% organic growth with all business groups above 10%, along with margins of 22% and earnings of $7.81 per share. Today, we are updating full-year expectations for organic growth to a range of 8% to 9% and EPS to a range of $9.70 to $9.90, reflecting our results to date and ongoing supply chain challenges. I would like to make a few comments on how 3M is actively managing those challenges. As you know, many companies are facing supply chain disruptions. The result of a convergence of issues including the Delta variant, strong demand, energy and labor shortages, and extreme weather events. For example, ocean freight costs have more than doubled over the last year, and the number of containers on the water is up 70% because of port congestion. Suppliers are challenged to provide consistent and predictable supply. On any given day, we are working with more than 300 suppliers with critical constraints. With manufacturing sites in 35 countries around the world, and as a $5 billion annual exporter out of the United States, we are working tirelessly to serve our customers. The cornerstone of 3M's response is our expertise and deep relationships across the supply chain, along with our local for local manufacturing and supply chain strategy, which helps us move with agility and keep our factories running. We have daily meetings with suppliers to strengthen our planning, and in some instances, are strategically prioritizing geographies and markets and portfolios, hard but necessary decisions to ensure we meet the most critical needs of our customers. We are moving product in different ways, such as expanding our use of rail, shipping out of more flexible ports, and increasing our use of charter flights by over 40%, while deploying new capabilities to better track our flow of goods in real time. Maintaining talent is also key, and we are using several tactics to attract new workers while protecting the health and safety of all of our employees. Some of our actions have impacted our productivity and gross margins, which Monish will touch on, but we will do what is necessary to take care of customers. The combination of strong demand, along with supply chain challenges, is also contributing to broad-based inflation. We are taking multiple actions to help offset inflationary pressures, including price increases, dual sourcing, and improving factory yields, with more work to do. Ultimately, the duration of these supply chain challenges is difficult to predict. We remain focused on serving customers, managing backlogs, and making good on our commitments. delivering the unique high quality products that are the hallmark of 3M. Please turn to slide five. While we execute day to day, we are investing to drive long term growth and capitalize on trends in large attractive markets. In home improvement, for example, we have multiple half a billion dollar plus franchises that keep families healthier and more productive, including our fast growing command damage free hanging solutions and Filtrete home filtration products. These brands leverage 3M's deep expertise in adhesives and nonwoven materials, the same technologies helping drive success in our automotive business, which consistently outgrows build rates. Auto electrification sales are up 40% year to date on the strength of new innovations, including advanced display technologies as automobiles become the next consumer electronic device. In healthcare, the biopharma market is growing more than 10% annually, with our business up more than 30% year-to-date, as 3M science has supported the unprecedented pace of advancement over the past 18 months to develop therapeutics and vaccines and scale manufacturing to help address the pandemic. The fundamental strengths of 3M are unique technology platforms, advanced manufacturing, global capabilities, and leading brands, position us to win, and we will continue to invest in these areas. In a similar way, we are driving productivity by advancing digital capabilities across our operations, allowing us to expand our use of data and data analytics. In sustainability, we have achieved 50% renewable electricity use in our operations, four years ahead of our timeline, on our way to 100%. We are advancing the environmental goals we announced earlier in the year, making the investments to accelerate our ability to achieve carbon neutrality, reduce water use, and improve the quality of water returned to the environment from our industrial processes. In addition, we are proactively managing PFAS, making our factories and communities stronger and more sustainable. In Cottage Grove, Minnesota, we recently announced that we are closing our incinerator. and partnering with a leading disposal company to more efficiently manage our waste streams. We just broke ground to add new filtration technology in Cordova, Illinois. In Zwijndrecht, Belgium, we are working with government officials to resolve issues related to PFAS and will invest up to 125 million euros over the next three years to improve water quality around our factory. These proactive initiatives and others are accelerating 3M's ability to go beyond current regulatory standards and deliver on our commitments. With respect to the PFAS strategic roadmap announced last week, 3M remains committed to working with the Biden administration, EPA, and others in taking a science-based approach to managing PFAS. Let me also touch on a few litigation updates. Last week, we announced a collaborative agreement to resolve litigation related to PFAS near a facility in Decatur, Alabama. The impact is included in our previously disclosed reserves. On combat arms, there have been four bellwether trials so far, with six additional trials here in the fourth quarter. We are early in this litigation and will continue to actively defend ourselves, including through the appeal process. As always, we encourage you to read our 10Q for updates on all litigation matters. To wrap up, we are driving strong results in a challenging environment, investing in attractive end markets and positioning 3M for continued growth. I am proud of our 3M team, which is united by a common purpose, unlocking the power of people, ideas, and science to reimagine what's possible and create what's next. Now we will turn it over to Monish, who will cover the details of the quarter. Monish.
Thank you, Mike, and I wish you all a very good morning. Please turn to slide six. As I look back on the quarter, the 3M team demonstrated the resilience of our business model and the relevance of our technologies as we executed well in a very challenging environment, effectively navigating the supply chain disruption while serving and innovating for our customers. Though manufacturing, raw materials, and logistics challenges persisted throughout the quarter, we continued to invest in the business while driving operating rigor and managing costs. Turning to the third quarter financial results, sales were $8.9 billion, up 7.1% year-on-year, or an increase of 6.3% on an organic basis. Operating income was $1.8 billion, down 6%, with operating margins of 20% coming in at the top end of the range, which we had previously communicated in mid-September. Third quarter earnings per share were $2.45, which was similar to last year. On this slide, you can see the components that impacted both operating margins and earnings per share as compared to Q3 last year. A strong year-on-year organic volume growth was more than offset by the headwinds resulting from the global supply chain challenges, investments in growth and sustainability, and litigation-related costs. Combined, these impacts lowered operating margins by 1.4 percentage points and earnings per share by two cents year-on-year. The restructuring program we announced in Q4 of last year remains on track. As part of this program, we incurred a pre-tax restructuring charge of $50 million in the third quarter. This charge was offset by the benefits we achieved this quarter. Moving to price and raw materials, as expected, increases in selling price gained traction as we went through the quarter, with year-on-year selling prices up 140 basis points in Q3 versus 10 basis points in Q2. However, we continued to experience higher costs for raw materials, logistics, and outsourced manufacturing, which outpaced the increase in selling prices. Thus, third quarter net selling price and raw materials performance reduced both operating margins and earnings by 130 basis points and 12 cents per share, respectively versus Q3 last year. Looking at Q4, we expect our selling price actions to continue to gain traction as we work to mitigate the raw material and logistics inflationary pressures we have experienced throughout the year. Next, foreign currency net of hedging impacts reduced margins 20 basis points and earnings by one cent per share. Also, three other non-operating items impacted our year-on-year earnings per share performance. First, Lower other expenses resulted in an 8-cent earnings benefit. Consistent with prior quarters, non-operating pension was a 5-cent benefit, along with a 2-cent benefit from net interest due to a proactive early redemption of debt. Secondly, a lower tax rate versus last year provided a 9-cent benefit to earnings per share. The tax rate was lower due to favorable adjustments this year related to impacts of U.S. international tax provisions. Our year-to-date tax rate is 18.8 percent. Therefore, we now expect a full-year tax rate in the range of 18.5 to 19.5 percent versus 20 to 21 percent previously. And finally, Average diluted shares outstanding increased 1% versus Q3 last year, lowering per share earnings by 2 cents. Please turn to slide 7 for a discussion of our cash flow and balance sheet. Third quarter adjusted free cash flow of $1.5 billion was down 29% year-on-year with conversion of 107%. Adjusted free cash flow year-to-date was $4.5 billion, which was similar to last year, with free cash flow conversion of 98%. The decline in our year-on-year free cash flow performance was primarily driven by higher inventory balances due to strong customer demand, along with raw material inflation and more goods in transit as a result of the ongoing global supply chain challenges. Third quarter capital expenditures were $343 million and $1 billion year-to-date. For the full year, we now expect CapEx investments in the range of $1.5 to $1.6 billion versus being at the low end of our prior range of $1.8 to $2 billion. We continue to step up investments in growth, productivity, and sustainability. However, the pace of projects continues to be impacted by supply chain and vendor constraints. During the quarter, we returned $1.4 billion to shareholders through the combination of cash dividends of $856 million and share repurchases of $527 million. Year-to-date, we have returned $3.8 billion to shareholders in the form of dividends and share repurchases. Our net debt position strong cash flow generation capability, and disciplined capital allocation continues to provide us financial flexibility to invest in our business, pursue strategic opportunities, and return cash to shareholders while maintaining a strong capital structure. Please turn to slide eight, where I will summarize the business group performance for Q3. I will start with our safety and industrial business. which posted organic growth of 6.1% year-on-year in the third quarter. Organic growth was driven by continued robust industrial manufacturing activity, along with prior year pandemic-related impacts. First, our personal safety business declined 4% organically, up against a 40% pandemic-driven comparison a year ago. Third quarter disposable respirator sales decreased 7% organically year-on-year and 15% sequentially. Looking ahead, we anticipate continued deceleration in disposable respirator demand through the balance of this year and into 2022. Turning to the rest of safety and industrial, organic growth was led by double-digit increases in adhesives and tapes, abrasives, and electrical markets. In addition, closure and masking systems was up high single digits. Automotive aftermarket up low single digits, while roofing granules declined against a strong comparison from last year. Safety and industrials third quarter operating income was $620 million, down 20% versus last year. Operating margins were 19.2%, down 650 basis points year on year. as leverage on sales growth was more than offset by ongoing increases in raw materials, logistics, and litigation-related costs, along with manufacturing productivity impacts. Moving to transportation and electronics, which grew 5.1% organically, despite the continued impact of semiconductor supply chain constraints. Our auto OEM business was flat year on year, compared to the 20% decline in global car and light truck bills. This outperformance was due to a few factors. First, we continue to grow our penetration by driving 3M innovation onto new automotive platforms. Second, we saw a notable increase in channel inventories at tier suppliers given the dramatic reductions in OEMs bill forecast through the quarter. Lastly, we benefited from a vehicle model mix standpoint as auto OEMs produced more premium vehicles, which tend to have higher 3M content. Our electronics-related business declined low single digits organically, with declines across consumer electronics, particularly smartphones and TVs, as OEMs faced production challenges due to ongoing semiconductor constraints and COVID-related impacts. These declines were partially offset by continued strong demand for our products and solutions in semiconductor and factory automation end markets. Turning to the rest of transportation and electronics, advanced materials and commercial solutions each grew double digits year on year, while transportation safety grew low single digits. Third quarter operating income was $465 million, down 9% year on year, Operating margins were 19%, down 320 basis points year-on-year, driven by strong leverage on sales growth, which was more than offset by increases in raw materials and logistics costs, along with manufacturing productivity impacts. Turning to our healthcare business, which delivered third-quarter organic sales growth of 3.3%. Our medical solutions business declined low single digits organically, impacted by the continued decline in demand for disposable respirators, along with the pace of hospital elective procedure volumes, which came in at the low end of industry expectations of 90 to 95 percent for the quarter. Sales in our oral care business grew low double digits year on year as dental procedures continued to be near pre-COVID levels. The separation and purification business increased high single digits year on year due to ongoing demand for biopharma filtration solutions for COVID-related vaccines and therapeutics. Health information systems grew low double digits driven by strong growth in clinician solutions. And finally, food safety increased double digits as food service activity returns. Healthcare's third quarter operating income was $529 million, up 7% year-on-year. Operating margins were 23.5%, up 70 basis points. Third quarter margins were driven by leverage on sales growth, which is partially offset by the increasing raw materials and logistics costs, manufacturing productivity impacts, along with increased investments in growth. Lastly, third quarter organic growth for our consumer business was 7.6% year-on-year, with continued strong sell-in and sell-out trends across most retail channels. Our home improvement business continues to perform well, up high single digits on top of a strong comparison from a year ago. This business continued to experience strong demand, particularly in our command and filtrate category-leading franchises. Stationery and office grew double digits organically in Q3 as this business lapsed last year's COVID-related comparisons. We also had strong back-to-school consumer demand and holiday-related sell-in for Scotch-branded packaging and shipping products, Post-it solutions, and Scotch-branded home and office tapes. Our home care business was up low single digits versus last year's strong COVID-driven comparisons. And finally, our consumer health and safety business was up high single digits as we lapped COVID-related impacts from a year ago. Consumers' operating income was $332 million, down 3% year-on-year. Operating margins were 21.7%, down 260 basis points, as increased costs for raw materials, logistics, and outsourced hard goods manufacturing, more than offset leverage from sales growth. Please turn to slide nine for a discussion of our full year 2021 guidance. As we reflect on the macroeconomic environment, we expect demand to remain strong across most end markets. However, uncertainty persists given the ongoing impacts of the pandemic, along with the well-known global supply chain, raw materials, and logistics challenges that all companies are working through. Looking ahead, we remain focused on our customers and doing what is necessary to serve them as we continue to navigate the fluid environment. Turning to guidance, we are increasing the bottom end of our expectations for organic growth. We now project a full year organic growth to be in the range of 8% to 9% versus a prior range of 6% to 9%. With respect to earnings, we anticipate a range of $9.70 to $9.90 per share as compared to our prior range of $9.70 to $10.10. And finally, we expect to continue to generate strong free cash flow. Therefore, we are maintaining our free cash flow conversion range of 90% to 100%. This updated outlook implies a wider than normal fourth quarter range, accounting for ongoing impacts of COVID and the uncertain supply chain environment. For example, from a growth perspective, the well-known constraints in semiconductor chip supply are impacting more and more end markets, most notably automotive and consumer electronics, as reflected in the low production forecast for the year. We anticipate global elective healthcare procedure volumes to stabilize with recent trends. Relative to disposable respirators, we expect continued impacts from the decline in healthcare-related demand, along with elevated inventory levels in the industrial channel. And finally, we expect our pricing actions to continue to gain traction as we work to mitigate raw material and logistics cost pressures. Turning to operations, as we have discussed, we are actively managing inefficiencies in global supply chains with a relentless focus on customer service. Therefore, we are adjusting demand plans with greater frequency and, as a result, incurring more manufacturing production changeovers along with expediting shipments. All of these actions are impacting both costs and productivity, but we are taking the necessary steps to ensure we meet the most critical need of our customers. We continue to make progress relative to December 2020 restructuring announcement. To date, we have incurred over $240 million in pre-tax restructuring charges and anticipate an additional $25 to $50 million in Q4. We now expect total pre-tax restructuring charges of $300 to $325 million, versus our original expectations of $250 to $300 million. We expect the remaining actions under this program to be initiated by the first quarter of 2022. In addition, we expect to incur higher costs related to our ongoing litigation matters, along with increases in other indirect related costs like travel expense. And finally, we continue to invest in the business for the long term, and therefore anticipate increased investments in growth, productivity, and sustainability. To close, I would like to take a moment to thank our customers who have placed their faith in us, our vendors who are tirelessly working with us to ensure continuity of supply, and most importantly, our 90,000 plus 3Mers who continue to deliver for our customers. We have a very steady eye on the long term to deliver growth, margin, and cash through strong operating rigor while continuing to navigate the uncertainty in the short run. With that, I thank you for your attention and we will now take your questions.
Ladies and gentlemen, if you would like to register a question using a landline, please press the 1 followed by the 4 on your telephone keypad. You will hear a three-tone prompt to acknowledge your request. If your question has been answered and you'd like to withdraw your registration, please press the 1 followed by the 3. If you're using a speakerphone, please lift your handset before entering your request. Please limit your participation to one question and one follow-up. One moment, please, while we compile the Q&A roster. Our first question comes from the line of Nigel Koh with Wolf Research. Please proceed with your question.
Thanks. Good morning, and thanks for the detail on the quarter. So, Manish, you mentioned the 19%, 20% margin for 3Q. You came in at the high end of that range. Obviously, you like to be conservative, but I'm just curious, what turned out perhaps better or maybe not quite as bad as you expected or feared back in mid-September?
That's a great question, Nigel. I think when I gave you the range of 19% to 20%, as we have said in my prepared remarks, we were facing a lot of inflation. At the same time, there was a lot of uncertainty as regards volumes, as regards supply chain flow. And then third, I'd also mention that as we were facing all those items, we were also doing our own self-help versus just letting these things go through, whether it was dual sourcing, whether it was controlling some of our expenses, et cetera. And when you put all that together, we came in at the 20%. If you look at where we ended up, I would say inflation came in pretty much where we thought it was going to be. We executed on price. We moved from 10 basis points of price increase in Q2 to 140 basis points in Q3. So that was pretty much in line. And we were able to execute more volumes. So with vendors, you know, with flow of supply, we were able to get good flow of supply. There's strong demand, as Mike said. And we were able to execute the demand. As well as we controlled our expenses across the corporation to make sure that we were prioritizing on serving our customers. and trying to mitigate the impact of inflation as much as we could. So put all that in, we came in at the 20% versus the range of 19 to 20 that I mentioned earlier.
That's great. Thank you. And on the margin bridge, based on your 4Q, your guidance, it looks like 4Q margins look to have an 18 handle. My math is off there, but I'd be curious if you can maybe to that, and maybe the two major margin bridge items, the volume productivity, supply chain, and price cost. 140 basis points negative on volume productivity and 130 on price cost this quarter. How does that look in a broad sense for 4Q year-over-year?
Yeah, so I would start by saying, Nigel, a couple of things. So your math is not way off. If you follow the implied guide that we gave you, it's directionally very close. I think a couple of things on just the items you talked about, which was price draw. We expect to continue to have continued momentum in price in the fourth quarter. You saw us again go up from 10 to 140 basis points, and we should see that go up as price continues to take hold across the various geographies and product lines. things that we have talked about before. I would say we don't see the raw material or the inflation environment slowing down in any way. I think you're going to see that volatility. It's going to depend on what the holiday season does. It depends on what logistics costs are going to be. Our goal is to get to neutral. The question is going to be how does raw materials at some point play itself out, and do we see a turn in some of the commodities like polypropylene, ethylene, et cetera, where we have seen a lot of inflation. I would say that's number one on your question. I think there was another point on bridge on revenue. I would just say if you're looking 3Q to 4Q, just remember there are a couple of things that impact 3M. There's one less billing day from 3Q to 4Q, and secondly, you have a normal seasonality that you have in 3M as many of the factories that are industrial customers slow down during the holidays, and that's the impact. So I think I've answered your question, but if there's anything else, I'm happy to answer.
No, that's perfect. Thanks, Manish.
Thank you. Our next question comes from the line of Jeff Sprague with Vertical Research Partners. Please proceed with your question.
Thank you. Good morning, everyone.
Hey, Jeff.
Hey, good morning. I just wonder if we could touch on auto a little bit. You know, kind of an extraordinary kind of divergence in the numbers there as you laid out. I just wonder, does that create some kind of significant headwind for you now as you look forward? Obviously, we should have volumes going up, but we have suppliers that need to burn off inventory and, you know, kind of mix shifts back. I just wonder if you could give us a little more perspective on what's going on there.
Yeah, Jeff, maybe there's a couple of parts to that that I'll talk about. The first, if you look at what we've done year to date, it's really been reflective of our innovation, something we've been talking about for some time. We outgrow the build rates, and even in a dynamic like this year where the build rates are swinging down as there were some challenges in the OEM production plans for Q3 and the outlook for Q4 being similar, we're continuing to drive our innovations, win jobs, you know, spec ins and design in opportunities. And then as Monish mentioned, the mix of vehicles in this kind of demand environment is more premium, which we have a higher level of penetration in those vehicles. We also have very good growth in our auto electrification priority growth platform and broadly and getting good traction, 40% year to date. So those are all driving that performance as we come through year to date and and we expect to be able to continue to outperform build rates as we go forward. The channel, everybody's challenged with matching up to the changes in production plans, and these are changing quickly, and the dynamic has been challenging for the supply chains and, I would say, everyone in the value chain to keep up with. That said, we see inventory trying to track pretty well with that. We don't see... Really, in our results, we're not seeing a year-to-date impact from excess inventory. So it's really about matching up with where the mix is going, where the build rates are going, and, again, we see good momentum in our portfolio against those build rates.
And just on maybe your CapEx and what you've seen your customers do, you know, when I heard Monish talk about seasonal slowdowns, You know, with everybody kind of running full out here and trying to get caught up, do you actually think it's possible we don't have a normal seasonal slowdown as people try to kind of execute on some of these backlogs? And kind of, you know, separate and a little bit unrelated, but your own CapEx, what sort of projects did you have planned that are sliding to the right?
Yeah, it's a good question, Jeff. Listen, we are trying to be helpful by giving you what we are seeing right now. Is there a possibility that customers continuing to keep running through 24-7 and that there's more production that comes out from them? Absolutely possible. And as Mike mentioned and so have I, we'll do whatever it takes to make sure that we keep serving our customers. Overall, I would still say this is a short-term phenomenon. Long-term, we are seeing good end market trends. And that's why you're seeing us continue to invest. So your point on the next piece, which is CapEx and where we were, I would say the areas where we are looking to keep investing were in all the three buckets, growth, productivity, and sustainability. And the cycle times to get CapEx raw materials for these businesses is just taking longer than we had originally thought, and that's why we had to slow it down to 1.5 to 1.6%. But I would just end your question by saying, Jeff, we are not done with the quarter. This team knows how to fight. We are going to keep doing whatever it takes to keep serving for our customers as long as the demand is there. And at the same time, the team is furiously working to make sure that we mitigate some of the raw material pressures that we have as well as keep investing for growth, productivity, and sustainability because we just see the long term to be very bright where we can grow above the macro, we can get margin expansion, and keep having strong cash.
Great. Thanks for the call.
Our next question comes from the line of Julian Mitchell with Barclays. Please proceed with your question.
Hi. Good morning. Maybe just the first question around China-Hong Kong demand. Obviously, 3M has a very large market. presence in the region, good perspectives on different industries. The growth rate, you know, slowed, I think, to 3% in Q3. You know, that was down from low double digit last quarter and low 30s in Q1. So just wondered, you know, do we think that China, Hong Kong may be down in the fourth quarter? And maybe just describe how you see what's going on there as being maybe different or idiosyncratic? Or do you think that that pace of slowdown is a good template for what we should expect elsewhere in the world as the demand recovery matures?
Yeah, Julian, if you step back and look at year-to-date, China's up mid-teens for us. So that's, I think, reflective of strong growth through Q3. And as you pointed out, we saw 3% in the quarter. I would say it's... having an impact from the same things we've been talking about, supply chain, logistics, foreclosures, those are impacting our business. And just as a reminder, our business in China, so we manufacture most of what we sell in China in factories in China. And we sell to customers, about 50% of them exposed to exports, about 50% to the domestic market. And the exports are probably one of the areas that's hardest hit. So it's down about 10%. looking forward. That's the expectation as we go forward to Q4. So that'll be one of the impacts. It's been one of the impacts being hurt most by the supply chain challenges. For us, our focus in China has really been very much in line with what we've been talking about as we came through the pandemic. We see market segments that are high growth, and we've been prioritizing investments there, and we see those growth trends continuing. So that's where we're focused. We're focused where we have kind of the winning solutions, and we do see opportunities across each of our businesses. Year to date, we've been led with strong growth in our healthcare business, or actually in Q3 in the healthcare business. We expect that to continue as we go into Q4.
Julian, just to add to Mike's point on all the items you mentioned on the macro trends, just on a year-over-year basis, too, for the quarter at 3%, you've also got to look at the comp of last year. We had a very strong growth in China. If you remember the third quarter of last year, uh you had seen china starting to come out of the pandemic first so their order patterns were higher in the end of like june and then into the third quarter and that's the other reason you see a three percent that's helpful thank you and then um maybe just my follow-up around um safety uh and industrial margins um you know understand what's going on with um
some of the markets in terms of supply chain constraints and the impact that's having on margins. But maybe focusing on the impact of the legal costs and also as the respirator business moves lower sequentially, you know, any color you could provide on the impact that those two things are having on margins, perhaps sizing that legal headwind. And do we expect that to bleed into next year as well? Thank you.
Yes, sure, Julian. There are two ones. On the legal one, the combat armed litigation that we are incurring costs on show up in the SIBG margins. As Mike mentioned, we are continuing to defend ourselves in that litigation. There's an acceleration in the fourth quarter. We'll have at least five more of these. for which we're going to prepare. So I would say, depending on how the litigation goes, do you see it bleed into 22? Yes, because the MDLs will all not be done by fourth quarter of 2021. On disposable respirators, as we have talked about, depending on seeing how the pandemic has played itself out, We felt Q1 was peak. We had mentioned that even in our last earnings call. We have seen revenue consistently, sequentially come down. You have seen we came down nearly 6% in DR in the third quarter. We see that further down between 75 to 125 on a year-over-year basis or 25 to 75 sequentially. And depending on where the pandemic goes, that will have an impact into 2022. But again, we are seeing pockets where you are seeing COVID cases go up, where you're seeing demand go up, and then in other cases, you're starting to see demand come down. So it's pretty dynamic on the disposable respirator side. But as we have talked before, we've got capacity of 2.5 billion respirators that we can ramp up very quickly. The team's done a really nice job of managing this environment. In certain cases, we have shut down manufacturing lines. In certain cases, we are managing our inventory levels as we go through this. But we'll be ready for the next factor event. And hopefully it never happens, but that's not been the history of the world. But we'll be ready for that.
Great. Thank you. Thank you.
Our next question comes from the line of Scott Davis with Milius Research. Please proceed with your question.
Good morning, everybody. Hi, Scott. The price increase in the quarter was a pretty dramatic quarter-to-quarter sequential change, but we've clearly seen pretty big step-ups in CPI and PPI. When you think about 4Q and kind of think about the ramp into 2022, Do you continue with this aggressive of a ramp? You know, is there any mitigating factors that kind of hold you back from getting price? I mean, I don't think I remember you guys being this far below CPI before, but, you know, these are strange times, too, so I'm not sure it really matters. Just some color on that ramp would be helpful. Thank you.
Sure, Scott. As I mentioned in my prepared remarks, you will see us continue to gain price in the fourth quarter. I know there have been quite a few questions around why it has taken us this long to get price. As we mentioned before, we follow a pretty methodical approach of taking price across geographies. We work with our customers. In certain cases, we are working with contracts and the constraints in those contracts. And we put a pretty thoughtful approach to how we go after price increases. How it goes into 2022, Scott, I think will also depend on where we see inflation going to be in 22 and beyond. Right now, I think we are comfortable with the price increases that we have taken, but we're going to keep doing it as long as we need to. As I mentioned, the goal of the team is to get to neutral, but it's going to highly depend upon what happens with inflation. So I don't know if I answered your question, but that's how we are thinking about pricing from that angle. And we try to be as Again, as I've said before, thoughtful and methodical in how we go about it. We have a pretty rigorous approach on how we approach our customers, and we try to work it as a partnership with both. And you've got different businesses. So you've got spec in businesses where you are spec'd in for a certain period of time. You've got healthcare where you've got half my business where it's easier to take price, in other cases that are contracts, and then you've got the industrial business, which is distributor-led, and then you've got the consumer business where we're working with all the big retailers. So each one of them have a different dynamic, and we factor all that in, and you've seen that we have made progress in Q3, and we'll keep making progress in Q4 and beyond.
Okay. Helpful, Manish. As a follow-up, and you know, the China comments were helpful, but can you talk about some of the other major emerging markets and what you've seen as far as, you know, improvements or decrements over the quarter and outlook?
Yeah, sure. Thanks, Scott. And just as a reminder, if you remember back to 2019, we aligned our businesses now around four go-to-market models globally. And so those businesses are executing global strategies locally everywhere around the world and each of them have a view of each of the regions. I'll give you kind of a view at the higher level. So we talked about Americas being up 7% in the quarter and low double digits year-to-date. The highest growth as we came through the quarter is in Latin America and Canada and up double digits across all business groups. So, again, similar to what we talked about in the way we're seeing year-to-date demand across 3M globally, broad-based across business groups in the Americas. and the United States still in a strong position, up 6% in the quarter and double digits for the year. EMEA, if you look at how we're doing there, we're growing high single digits for the year, 9%, 4% in the quarter. We haven't seen as strong a rebound in growth as other areas, but we are seeing a recovery now in health care and transportation and electronics starting to help drive that growth that we are seeing. And in Asia-Pacific grown mid-teens year-to-date, double-digit growth across the business groups, all business groups again. And as I mentioned, we talked about China a bit. I mentioned Japan in prepared remarks. That's been one of the improving areas is Japan now starting to see improving growth as we come through the year. So not down, not near the pre-COVID levels yet, but again, starting to see some improvements. And in that case, also being led by healthcare. So we're seeing some I would say the recovery of the elective procedures around the world being one of the dynamics that's helping to start driving improving growth.
Thank you. Good luck, guys. All right. Thanks, Seth.
Thank you. Our next question comes from the line of Dean Dre with RBC Capital Markets. Please proceed with your question.
Thank you. Good morning, everyone. Hi, Dean. Hey, we've heard lots of specifics on material costs, inflation, I'd like to hear some color on labor costs, labor shortages. I know, Mike highlighted in the opening remarks about new initiatives for recruiting, I'd imagine, higher comp and benefits are among those. And is this more of a US centered headwind? Or just how's labor costs and shortages look globally and start there, please?
So I would say, Dean, it's a global item, but it's more pronounced right now for us in the U.S. So we are seeing higher costs, whether it is cost driven by some of the items Mike mentioned, as well as with the demand that we have, we are spending more money on overtime. And also we are seeing cost of inflation, which is labor cost that comes to us through outsource manufacturing, hard goods, the hard goods that we buy. We are also seeing inflation on that. But with that said, I do want to recognize all the employees of 3M who are tirelessly working to make sure that we are delivering for our customers in this tough demand environment as well as a very tough supply environment. But we're confident, Dean, we'll get through this.
Do you have a year-over-year labor cost, any kind of specifics you can help us with?
I don't have it very specific. I can ask Bruce to follow up and give you an answer. But just if you go back to the bridge on the walk for Q3, you can see there's 140 basis points of pressure due to organic volume and productivity. Some of that is driven by labor constraints, in other words, the higher cost, but at the same time making sure that we have all the production that we can make. And some of it is driven by the fact that we've had to have more changeovers because raw material has not been flowing properly.
Got it. And just as a follow-up on the go back to litigation, I was hoping you could comment on the strength of your insurance coverage, whether it's PFAS specifically. We'll see headline settlements. What we don't always have line of sight on is the insurance coverage. Are there any coverage limits? And just help us, frame for us the strength of the insurance coverage, if you could.
Yeah, so we do have insurance coverage. We are working with our various insurance providers through multiple dialogues that we keep having with them. But as you know, some of these things take time. So when we do get those settlements in, we'll definitely keep you all posted.
Okay, thank you. Thanks.
Thank you. Our next question comes from the line of Andrew Obin with Bank of America. Please proceed with your question.
Good morning. Hey, Andrew. Hey, Andrew. Hey, this is a question, sort of a bigger picture question for Mike and maybe Manish. You know, I think 3M has a fairly unique integrated model, and, you know, the way your supply chain flows internationally, I think, inside the company is also fairly unique. Do these, you know, current supply chain constraints and shipping constraints, sort of, A, give you an opportunity to re-evaluate, you know, how your internal supply chain are constructed. And, yeah, I'll just leave it at that.
Yeah, Andrew, it's One of our fundamental strengths, and back to what Monish was talking about, how we're focused on delivering for customers, we're leveraging the strengths of our 3M model, the idea that we talked about in the prepared remarks, local for local, building our capabilities across our value model to the customers close to them regionally around the world. And that has been a strength as we've come through COVID. And I would say this year, as we deal with the interruption of the supply chain, this This regional strategy has allowed us to be more agile in just what Monish was talking about, the changing nature of our production plans and our production wheels and what we're doing in our factory. So we have a lot of flexibility built in. I would say we're always evaluating how to better serve customers. How do we look at our lean value streams end-to-end? How do we take new strategies into that? Based on, I would say, the improving visibility we have, we see opportunities – to be more efficient and improve our cycle times and so on. So we're always looking at changes. I do think the model that we have has served us well, and it's been a great place to respond to the challenges. And I think that's the foundation as we go ahead, is how do we make that better? How do we drive better performance, improving operational efficiency? So building on those strengths is where I'd leave you with.
Thank you, Mike. And just a follow-up question, and I apologize if I missed it, but on elective procedures, what's your best guess with sort of falling COVID cases in the U.S.? You know, what's the most likely trajectory for elective procedures over the next, you know, let's say six months?
Yeah, so Andrew, that's one, of course, we keep watching very closely. We, for the quarter, we ended up at, I think the industry ended up at a lower end of the 90 to 95% that was originally forecasted. Part of it was, I think September was a tougher month as many countries saw a spike in COVID cases. Our belief, and I think it's the industry's belief, that we should stabilize in the fourth quarter and hopefully get back to the 90% to 95% range as we get into the fourth quarter. And then the bigger discussion around the industry is what does 2022 and beyond look like? The reason is a lot of these elective procedures that have been slowed down are elective, but they're still time sensitive at the end of the day. So that's what we'll have to see and see what capacity is added in all the countries. We have to see how cases play out from a COVID perspective. But I also think hospitals are far better equipped right now or more prepared to deal with this. So our hope is that elective procedures come back up to 2019 levels in 2022. When it happens, I think will depend on different parts of cases in the world. But that's how we see it.
And do you see a possibility of a cumulative catch-up in 2022?
Well, I think that's the debate, right? Who knows? But I think that's going to depend basically on hospital preparedness as well as patient readiness to come into the hospital to get their surgeries done. From our end, you know, we would rather have the volume than not have the volume. So, you know, I would say it would be a good problem to have, but I think we'll have to see what happens.
Thanks a lot, guys. Good luck.
Thank you. Our next question comes from the line of Nicole DeBlaise with Deutsche Bank. Please proceed with your question.
Yeah, thanks. Good morning, guys. Hi, Nicole. I just wanted to dig into what you guys are seeing from a supply chain perspective a bit more. So if you could talk about, you know, any changes in the key bottlenecks versus last quarter's update, and is there a sense at all that there's green shoots here, meaning that Is there any possibility that the supply chain issues or headwinds have peaks?
Well, Nicole, I'd go back to it really is a convergence of multiple factors, and so you've got to pull those apart a little bit. The strong demand we think will continue to see strong demand, so that's going to put pressure on the supply chains going forward. We've seen challenges in labor shortages. The pandemic has impacted production. The semiconductor shortages are impacting end markets for us in particular. And then we were also impacted as we went through the year with some extreme weather events, which interrupted our raw material supply. Those are getting better. So some of the raw material supply issues that we were facing are getting better as we go. And we do expect supply chains to improve. It's difficult to... estimate or predict the duration of each of these factors and how they play with each other. Watching the congestion and logistics is one of the things that we are carefully looking for improvements in as well. Can we move back to more normal logistics patterns for us as we go forward? That will be a good sign that broadly supply chain disruptions are improving. But you'll have to keep an eye on each of these aspects to see step-by-step. And we are optimistic. We are hopeful as we get into 2022 that we're going to continue to see improvements.
Nicole, we also have a control tower that has been set up, so we are constantly watching whether it is the port congestion, whether it is shutdown of airports, whether it is customers or suppliers telling us that raw material may be a few hours late. So that's why we are changing in our factories faster to keep other products moving so that we just make sure that we keep customer demand as well as customer demand itself is pretty variable right now. And that's another big thing that Control Tower is doing is watching customer demand and then adjusting supply as needed.
Got it. Thanks, Manish. Thanks, Mike. That was helpful. And then I guess for 4Q, as we kind of think about the expectations by segment, we've kind of discussed elective procedures within healthcare. You guys talked a little bit about safety and industrial and what's going on with masks. But I think both consumer and T&E are facing tougher comps in the fourth quarter. Is the expectation that those businesses can still grow organically or is there a risk they could be down year on year?
So I would start with just transportation electronics. You know, that business is impacted the most by two. One is the auto industry, and second is the electronics industry, and the semiconductor shortages hits that business squarely. I would say on the auto bill, the latest IHS forecast that we look at is on a year-over-year, 20% down is where auto bills are expected to be. There's also, they're facing comms from last year in the electronic side, so whether it's consumer electronics, TVs, tablets, all of them are supposed to be down on a year-over-year basis. I think we'll have to see where semiconductor shortages land up for that business, but the Ashish and team are fighting hard, and if the volume's there, they're going to do whatever it takes to make sure that the customers are served. On consumer, you're right. That's also facing very strong calm from last year, but you can see what Jeff and team have done. In the first 11 months, we have seen strong growth. Our platforms, whether it was Command or Filtrate, our Post-it notes, et cetera, all have seen good growth in the third quarter. We saw a good early start in our stationary business in the holiday season. The question is whether that continues is the thing that we'll have to keep watching.
Got it. Thanks. I'll pass it on.
Thanks. Thank you. Thank you. Our next question comes from the line of Steve Tusa with J.P. Morgan. Please proceed with your question.
Hey, good morning. Hi, Steve. Hey, guys, so what is, like, the underlying, like, leverage this quarter? Back out price costs and then I think, like, the year-over-year on restructuring costs and savings and then temporary costs. kind of mask things a little bit, but if I just, if I kind of like back into it, I'm getting something negative on the revenue growth. But then obviously there's, you know, the supply and, you know, that other inflation that you have to deal with. So what is like the underlying, is the underlying leverage positive this quarter on that 5% or was it negative because of mix? Like just kind of hash that out a little bit because a lot of moving parts here.
You're breaking up a little bit, Steve, but I think I got your question is what's the underlying leverage? And I would tell you it's a little hard for me to X everything out from a restructuring perspective, X out organic volume, price draw, and then give you a leverage. I would just tell you when you look at the bridge that we have given you, we did see volume growth. but that was offset by the productivity from global supply chain as well as growth and productivity and increased litigation costs. And you can see that hurt us 1.4% on that productivity basis. That's the way I look at it, Steve. It's very hard, and I think it would be unfair for me to just X everything out and then tell you leverage is good because I don't think that's the way we look at it. Because for me, ultimately, it's the all-in, what I give you versus X-ing stuff out.
Right. I guess, like, is there a reason why you wouldn't be able to convert more normally in, you know, 22? I guess, you know, assuming these things stabilize. I mean, is this business still a, you know, a 35% kind of core incremental margin business?
I would say so, Steve. I think, again, you have to go back to all things being equal. Yes, it's a 30% to 40% leveraged business, and I don't see that changed. But I think it will come down to what does supply chain trends look like in 2022? You've seen not just us, but many of our peers as well as other people have said supply chain constraints go into 2022. But I think long term, as Mike has mentioned and I've said, we are very confident we can grow above the macro, we can get margin expansion, and we can continue to have strong cash. So all those, I think it's just a short, uncertain time that we'll have to just see how supply chain plays itself out.
Yeah, yeah, very appreciated. Okay, thanks. Thanks for the help.
Yep. Thank you. And our next question comes from the line of John Walsh with Credit Freeze. Please proceed with your question.
Hi, good morning.
Hey, John.
Hi, John.
Hi. Maybe just first a question around the restructuring of I think you used the term on track, but I just wanted to confirm the numbers here. I mean, the prior program was $275 million of cost, $225 million of savings, and then now you've taken it, obviously, up higher here. How do we think of it? One, is that what you mean by on track? That's kind of like an 82% conversion on the savings and On the new actions, how do we think about the payback on those?
Yeah, so I'll reiterate. Our program was going to cost somewhere between $250 to $300 and benefits of somewhere between $200 and $250. what we have looked what i said in this uh in my prepared remarks was year to date we have spent 240 million against the 250 to 300 and we are up that updating that from from 250 to 300 to 300 to 325 and we largely expect the program to be initiated by the end of 1q 22. on the benefit side We are, we had set 200 to 250 with all the actions that we have taken. We see ourselves at the higher end of that range in between the 225 and the 250 with half of it that's already shown up or will show up for this year in 21 by the time we're done with the fourth quarter and the balance will show up in 22.
Yeah, John, I just want to clarify one thing. Monash that year to date, we've had $240 million of charges. That's actually $140 million last year in Q4 and $100 million year-to-date this year.
Sorry, program-to-date. And as you know, John, we don't remove restructuring charges from our results, and that's all included in the numbers we report. So we don't adjust for that.
Yes. No. Thank you for the extra details there. And then maybe just as a follow-up here, a lot of questions around supply chain. I think we're all following the semi-shortages, et cetera. But 3M, you also mentioned probably propylene and some other supply chains that are a little bit more ancillary to kind of semi and some of the things we might be tracking day to day. I'm assuming there was some impact there from either hurricanes, force majeures, et cetera. Can you maybe just help us understand what you're seeing in that part of your supply chain and how long the duration of that might be?
Yeah, so we are seeing polypropylene ethylene resins, all of the ones other companies have mentioned, seeing inflation. Many of these are crude derivatives. They are not perfectly tied to the price of crude, but you can see where crude is going, so there's derivatives. They all have got impacted all the way in February with the hurricane that happened, and then I would say the global supply chains have further put pressure on it for the material flow across the globe. And that makes it harder for you to buy material only in certain locations. And just, I would, if my memory is right, on polypropylene and ethylene, we saw actually a jump in August. We've seen it come down a little bit in September. But that's, again, it's a demand-supply equation there. But it all goes back to Hurricane Ida that happened in February. And then the demand... from the pandemic also increased the need for the product. And all that put together, Mike used the word convergence, has driven some of the pressures on the chemical side of the house.
Great. Appreciate you taking the questions.
Thanks, John. Yeah, thanks, John. Thank you. Our next question comes from the line of Andrew Kapowitz with Citigroup. Please proceed with your question.
Hey, good morning, guys. Morning. Just maybe an update on how you're thinking about cash deployment. At this point, I think we all understand your priorities, and they start with organic investments. But at what point do you ramp up your purchases? For instance, if your stock continues to languish a bit on door, at what point do you think you've gone far enough into a salary integration so that 3M might be better equipped to make a larger deal again?
yeah so i'll just again just i uh and my apologies and i am just going to reiterate our capital allocation priorities just so that everyone's on the same page our first priority is always go organic we just see it's the best use of our capital best return as you can see we are not afraid to deploy capital we've done that in 2020 we are continuing to do that in 21 which is investing in growth productivity and sustainability We were going to spend $1.8 to $2 billion this year, but with some of the supply chain constraints, it's down to $1.5 to $1.6. But we still believe in the long-term growth, and so we're going to keep investing in that. As Mike had announced early in the year, we also announced $1 billion to improve for our sustainability efforts. That's going to be spent over the next 20 years, but it's front-end loaded, so that's the second piece on organic investment. Dividend is our second priority, important for our shareholders, so that's a priority that we clearly are focused on. Our third priority is M&A, and you're right that we are integrating Accelity, and the team's doing a very nice job by integrating Accelity into our business. At the same time, we have tons of ideas and we have a pipeline that we will execute when we see that we get a target that we believe can add value to our shareholders. At the same time, it's things that we believe that we can add value to the target too by using some of the strengths that we have, which is our brand, our global capability, our employee base, our material science capability, et cetera. So that's our third, and we always have an active pipeline. And then the last one is share buyback. You've seen we have now done $1.3 billion for the year. We did $527. That's the last priority for us from a deployment of capital perspective. But, you know, depending on the stock price and how much cash we generate, we clearly will look at that, too. Overall, I would just say when I look at net debt to EBITDA leverage, which is at approximately 1.3, at that point, it goes... gives me a lot of financial strength and optionality. It gives 3M a lot of financial strength and optionality. So depending on what opportunities we see, we won't hesitate to deploy capital because, as Mike mentioned, even some of the platforms that we've talked about, all of them are GDP plus growth platforms. So that's an area we would love to keep investing in.
Manish, that's helpful. I mean, could you give us a little more color on what's going on in your healthcare business in terms of margin and I think margin performance is relatively good year over year, at least versus your other segments. So how much is the salary integration helping? Is it a mix of your businesses such as oral care outperforming that's helping margin? And how are you thinking about the margin trajectory in that business moving forward?
Yeah, so for healthcare, I also look at EBITDA. If that helps, Fendi, I think year-to-date we are approximately 31% on an EBITDA basis. The team, most end team, have done a really nice job of continuing to drive margin. We increased margin 70 basis points in the third quarter. I would say it's a performance all around. The oral care business and the SNAP PAC has definitely helped. It helps us on a volume. It helps us on leverage with the volume in the factories. The MSD business, if you exclude the disposable respirator decline, grew very nicely in the second quarter, and MSD is where Accelity is in there, too. Accelity was impacted in the third quarter by lower elective procedures, but the integration is going well. We're continuing to find synergies between the cross-selling that we can do with our wound care business and Accelity, or our existing wound care business and Accelity. We are very happy with that progress, but in the spirit of continuous improvement, there's always more we can do here to drive growth and margin, and most of our team are very focused on continuing to do that.
Appreciate it, Manish.
Thank you. Our next question comes from the line of Joe Ritchie with Goldman Sachs. Please proceed with your question.
Thank you. Thanks for fitting me in to everybody. So maybe just on the price-cost discussion, I guess you haven't covered you guys for a while. It's rare to see that price-cost equation negative. I guess the question I have is, do you think we're at the peak of pain, that 140 basis point impact on price-cost? And then my follow-on to that is, Munish, you talked about some of your, you know, some of your business being going through contracts. I'm just curious, like what portion of your business is tougher to reprice in this environment?
So to answer your first question, we have made progress on price. You saw us going from 10 basis points to 140. And if you recall, Joe, we had said that you will see this ramp through the year because we take a very methodical approach to driving price across the multiple geographies and the channels we have. We should continue to see progress in the fourth quarter as these price actions that we have taken in the third quarter continue to take hold. I think the big issue that we have seen is inflation has come in faster than anybody thought. And so the team has continuously done what it can to drive price increases. To the question that was even asked earlier, our goal is to get to neutral of price and raw. But I think it will all depend on how inflation goes. But the team knows how to drive price. The team knows. drives a lot of innovation that also helps from a price increase perspective. So all that put together, the team's working it pretty hard.
And I guess the question on the contracts and being able to reprice some of your contracts, do you have some kind of benchmark for us on what portion is a little bit tougher to reprice in this environment?
Yeah. Listen, all price increases, we work with our customers. We have contracts with many of our customers. In some cases, we give 90 to 120 days notice. In some cases, these are longer contracts that we work through. And then we have spec in businesses that we work directly with OEM. So put all that together. That's how we look at this. So it's hard for me to give you one number because Pick a day, and I think you'll have a different percent of contract under contract, quote, unquote.
Got it. Okay. Thank you very much.
Thanks, Joe. Thanks, Joe.
Thank you. That concludes the question and answer portion of our conference call. I will now turn the call back over to Mike Roman for closing remarks.
To wrap up, our team is performing well in a challenging environment, delivering broad-based growth, good margins, and strong cash flow. We will stay focused on managing supply chain constraints, investing in attractive market trends to drive our growth, and creating greater value for our customers and shareholders. Thank you for joining us.
Ladies and gentlemen, that does conclude the conference call for today. We thank you for your participation and ask that you please disconnect your line. Thank you.