This conference call transcript was computer generated and almost certianly contains errors. This transcript is provided for information purposes only.EarningsCall, LLC makes no representation about the accuracy of the aforementioned transcript, and you are cautioned not to place undue reliance on the information provided by the transcript.
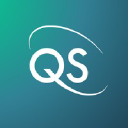
QuantumScape Corporation
5/11/2021
process where the firm's just run through a continuous flow heat treatment tool that ends up processing those at the right heat profile. So those are the kind of things that we're doing and that we need to keep doing. At the end of the day, the measurement of that comes out to, are we able to deliver the cells that we are planning on delivering to our customers? So if we could, for example, have a QS0 produce 200,000 cells a year like we're planning on, then that would be an indicator that all those metrics are, in fact, tracking to our goals.
Yeah, that makes sense. And just lastly, I was hoping you might be able to just pass along what you're hearing from other OEMs aside from Volkswagen on the developments since you've made them public. Some of them seem to still be very focused on silicon anodes with conventional separators and electrolyte. Are they conveying that that's kind of a temporary solution, or are you hearing more interest from others at this point?
Well, I mean, what we're hearing is exactly that, that people, you know, clearly silicon is here today and has been here, frankly, for a while. So, you know, one thing, sorry, a couple points. One is that silicon is here today, so there's no reason not to use it. But I think there's, you know, of the people that we've spoken to, there's general agreement that lithium metal is the endgame. In fact, those are some of the words that we hear from the OEMs directly, because you can't have a theoretically high energy energy density or specific energy anode than pure lithium metal in the sense that lithium metal doesn't have any host material. So all you have in a lithium anode is the same lithium that's cycling back and forth. Assuming, of course, it's zero lithium cells. There's no excess lithium in there to help the nucleation of that lithium anode. So with zero lithium, the only lithium in the anode is one that's cycling back and forth. You know, there's no silicon, no carbon, nothing else to weigh you down or take up space. Now, the second point about silicon is the reason why silicon is a little bit, you know, a nebulous thing to get your object on is because, you know, When people say silicon anode today, what they're really talking about is some amount of silicon that's actually put into a carbon anode. So it's a carbon anode with some level of silicon in it. It's never 100% pure silicon. And the reason for that is, as you I'm sure know, is pure silicon absorbs a lot of lithium and expands by a factor of four, roughly speaking, and then contracts again when that lithium goes out as a cell is discharged. So they've been charged and discharged. Lithium is already expanding and contracting like a sponge soaking up lithium. I'm sorry, silicon is expanding, contracting like a sponge soaking up lithium and letting it go. And over repeated recycling, that silicon pulverizes itself, resulting in a loss of capacity. So the only way to prevent that that people have come up with is to have a small amount of silicon in the carbon anode. And so there's a direct trade-off. with silicon anode could mean how much silicon you have, which corresponds to energy density, and your cycle life, which results from the polarization of that silicon. So when people say silicon, it's important to ask, well, how much silicon are you talking about? Because 100% silicon solution, to our knowledge, has never been shown to have any kind of decent cycle life. And this is, unfortunately, one of the things that sometimes You know, not reported in a way that's easy to understand. Some companies on the silicon side will sometimes report data where they'll show energy density of a silicon anode with a higher amount of silicon in it, and then they'll show a cyclized slide with a lower amount of silicon in it. And it leaves the leader uncertain as to whether it's the same cell or not. It's important to kind of be able to ask those questions so they understand what's being said. So for the net of it is that, yes, the OEMs that we're talking to are all looking at silicon as an intermediate step towards the endgame of a pure metallic lithium anode if that can be done. Obviously, we haven't yet shipped them pure lithium cells to put in their cars, but if we do that, then we expect to see very strong interest in that from multiple OEMs as opposed to continuing to use silicon anodes.
Great. Thanks, Dr. Deep.
Thanks, Rod.
Your next question is from the line of Mark Delaney with Goldman Sachs.
Yes, good afternoon, and thanks very much for taking the questions. Maybe first to follow up on that last question, the shareholder letter talks about continued strong and valid interest from multiple prospective customers. Could you elaborate any more on that in terms of how the inbound interest the company is seeing currently maybe compares to how it was as of the last time we spoke about 90 days ago, and what it may take in order to win an additional customer beyond BW?
Hey, Mark. Thanks for the question. We obviously can't comment on any deals that aren't announced, but we have said that there's been a lot of interest from a lot of players. Since we announced our batting showcase results in December, since we announced our Q1 earnings call with the market year results, we've seen a continued increase in interest both in terms of the level of interest and the amount of interest in terms of the number of players out there in our technology and our solution. And to be candid, right now, We really expect to be supply constrained in terms of both near-term delivery of test cells to these OEMs as well as the prototype samples that will come off of our QS0 pre-pilot line. We did, as you know, decide to expand the QS0 pilot line more than double its capacity. That was a key part of the reason to do a follow-on operating last quarter. But even with that added capacity, We expect that we'll be on allocation, which is a good problem to have in some sense, but it's still a problem in that we can't serve everybody's needs. The reality, Mark, is that we're, as a company that's still emerging, we won't have the management bandwidth to have too many customers in terms of our ability to support them. So we're going to have to pick a small number of key partners anyway. But in terms of the amount of interest we're seeing, I would say it's very broad, as you would expect. I mean, if you have a technology that has the kind of features we're talking about, high energy density and the ability to charge more quickly, and some of the safety benefits in a solid-state separator in the cycle life that we're talking about, then why wouldn't it be attractive? So our key challenge really is delivering enough cells to all these players to try to give them what they need, and we'll end up really prioritizing the ones that we think will be the best fits for what we're doing.
That's helpful. Thanks. My second question was trying to better understand a comment in the shareholder letter. It talks about targeting commercial production in the 2024 to 2025 timeframe. And I'm hoping to understand how that compares to the analyst day presentation showing about a quarter of a gigawatt hour being shipped in 2024. And I think that was pretty early production. So maybe there's no change, but just trying to better understand the current phrasing compared to what had been previously articulated on the financial plan. Thank you.
Yeah, I think you pretty much articulated it well. If you look at the analyst presentation, the model that we had there, it showed relatively small revenue in 24, wrapping up in 25, and that's what we're referring to when we say 24 to 25 type thing.
Okay, thank you.
Your next question is from the line of Ben Callow with Baird.
Hey, thank you, guys. You know, John, you do a very good job of explaining stuff that's very complicated to lay people like me. You said something about, you know, the cells and, you know, ramping up a battery factory at 18 to 24 months. And I was wondering just how the difference is in, you know, the form factor, you know, as you go, you know, you know, from a cell to a battery and put that into a pack and the kind of equipment that takes and the, uh, I would assume that you did a diligence with VW about that step, taking all those different form factor cells and making it into a pack. But if you can just maybe explain a little bit more to make it really neat for someone like me. Sure.
No, absolutely. A great question, Ben. So a couple of points of context before I even answer the question. In terms of the factory itself, much of the tools that go into the factory are actually going to be very similar to what goes into a lithium-ion conventional factory. So for example, the capital line, will be virtually the same. It's going to be cathode-coated from the same types of suppliers. The cathode active material will be very similar to what's already used in today's or the upcoming generation of lithium-ion batteries. The anode line, as you know, doesn't exist because there's no silicon, no carbon, not even an extra layer of lithium on the anode. It's purely a zero-lithium anode that forms in situ in the first charge. So we keep the same cathode line and we eliminate the anode line. The only difference then is that where the conventional battery buys separators from separator suppliers, we make our own separator. However, even there, we make that separator using tools that are scalable and continuous . So there's a two-step process to making that separator. is a casting process very similar to what's used for cathode coatings. So it's already obviously very scalable tools. And the second step is the heat treatment step. But that, too, is a continuous flow heat treatment tool where things are running through this conveyor belt and being handled in a continuous flow fashion. So they're both very scalable processes. The second part of the question is, how is the battery or the battery pack process different from the cell process? So when we started the company, we actually thought we might end up making both cells and packs. We since realized a couple of things. One is that making sales is hard. So we decided we wanted to focus on sales and not take on additional tasks beyond that, like the pack. But secondly, we also found that the OEMs we were talking to very much wanted to control the pack themselves because the pack is an integral part of the vehicle design itself. It's integrated very tightly and mechanically, thermally, electrically via software. So they very much saw the pack as a part of the car. The nice thing about making cells, however, is cells have a very simple interface. A cell is a two-terminal device with not a lot of other complexity beyond it. And so when we make cells, it's easy to hand off to the OEM. The OEM is the one who makes packs. So really our only responsibility is at the design phase to make sure that we communicate the external behavior of the cell. That means its electrical interface, the thermal behavior, the interface to the vehicle in terms of BMS and so on. But that's all we do. And the actual delivery of parts is just cells. So we just deliver cells to them, and they will engineer the pack that can accept those cells and build a full pack with them.
I guess just to round that question out, so someone's already, BW, and then your next OEM partner is already developing that pack, right, to match the cells? and the next cell that you do looks bigger?
Yeah, so actually the way it works is it's a collaboration. So the OEM tells us what their module impact looks like and what kind of cells would fit that module impact. And we design a cell that is designed to fit into that module impact with minimal change. So in effect, This is why, you know, when people ask us how many layers on your cell, we say the actual layer count depends on the particular OEM because every OEM has a slightly different, or in some cases, quite different module and pack architecture. But we actually, you know, modify our cell design. So when I talk about the commercially relevant form factor being roughly the size of a deck of cards, the reason why I say roughly is because the precise dimensions may vary by OEM in order to more cleanly fit into their module and pack.
Got it. That's very helpful. Congrats on raising the money. That was good. Could you talk maybe about, you mentioned the VW and I think the milestones in the report, just the housekeeping aspect. Is there another milestone that triggers capital injection?
Yeah, so the answer is that particular milestone was set back roughly a year ago when we entered into our Series F agreement with them. This was before, obviously, we were a public company. We were still a private company, and they were participating in the private round that we were doing at the time. And they had committed to invest $200 million. The first – and this is, of course, COVID had already started, and so – The automotive OEMs have seen a significant drop-off in their revenues and cash flows, and they had requested the idea of having a two-tranch investment approach. Tranch one would be in December with no closing conditions, just simply a time delay to allow them to manage COVID impacts. And the second tranche, they wanted to have that tied to what they thought was a really significant milestone on the path to commercialization. And that milestone, as we report in our shown on the letter had to do with a specific form factor and specific test conditions. And the form factor there was important because that specified near production thicknesses and areas for the separator itself. So that gave them confidence that, in fact, we can make these separators in the right level of thickness to be commercially viable and achieve our energy density goals. And then on the test conditions, but they specified a specific test of conditions relative to temperature and rate of power and number of cycles and so we were very pleased when the cells met all those conditions and that just unlocked the kind of money that was committed to a year ago but now now that's fully funded so uh the um the only further uh cash coming in from VW is going to be related to putting in place this joint venture that we've talked about in the past where they've committed an undisclosed sum to fund a 50% share of the first production plants that we're doing in this JV.
Got it. Thank you very much for the transparency. Thank you.
Thanks, Ben. Appreciate the questions. Your next question is from the line of Joseph Spack with RBC Capital Markets.
Thank you. Good afternoon. Clearly good news on the larger format four-layer cell test. I was just curious, though, like, was this one test or, like, how many four-layer cell tests were done? And I guess related, like, I know these are still, you know, pre-production cells, but, you know, how difficult or what was the yield to sort of get the larger cells for the test there?
Yeah, thanks for the question, Joe. So, yeah, this is definitely good news, though, because As you point out, on the last earnings call, we reported four layer cells. But because we didn't have the capacity, we made them in 30 by 30 millimeter form factors, which is somewhat smaller than this 70 to 85 millimeter commercially relevant form factor, kind of the playing card size. So the question was, OK, great, we can make them work in 30 by 30 form factor. What happens when we scale up to the full playing card size fall factor? Will they still work, or will new problems creep in? And so what we reported on this data you see in the slide in the show of the letter is, in fact, that when we made them in multilayer cells, and this is more than one cell. We always make cells in batches and put them on tests in batches. And obviously, the yield is not 100%. So when we make the cells, There's some cells that don't make it out of the manufacturing process, but of the ones that we deem to be good cells, we see very good performance in terms of cycle life and capacity retention. On the slide here, you're seeing that it's hard to read because we don't have a background grid on the slide, uh that you see that these cells are approaching 500 cycles now with i think around 90 capacity retention which means if they continue on uh in this fashion uh you expect over a thousand cycles about 80 percent in the full 70 to 85 millimeter size four layer cells so that's that's definitely you know uh new news and it's good news uh because it means that that when you it's what we showed last time was when you stack four layers up together You don't adversely impact cycle life. And now what we're showing is when you increase the area of those four layers, you don't impact the cycle life or capacity retention. And those are the key questions that we had was, you know, are there... strange interaction effects. So, in fact, you have larger area. Does that create a bigger opportunity for problems to creep in and so on? And what this data shows is that it is, in fact, possible to make these polar cells and have them perform really well relative to cycle life and capacity retention. And again, all these tests are being done at aggressive rates of power so one hour charge and one hour discharge uh battery cycle like testing is not done at those rates uh typically done at c over t so three hour charge and discharge uh this is more like again one hour charge means you're discharging a full multi hundred mile range car in an hour right so that's hundreds of miles an hour in terms of what you're driving, and then you're also recharging it at a supercharger in an hour as opposed to, you know, in your garage overnight. And then these tests were done actually at 25 degrees Celsius, which is, you know, basically room temperature, which, again, is something that isn't typically seen in solid-state systems. So we're actually very pleased with the performance that we're seeing here. Again, we're very careful always to emphasize that, you know, whenever we hit a milestone that, you know, that it's a milestone, there's more work to be done, right? We got to get to the eight to 10 layer cells. Uh, you know, the question that a lot of us, we have to, you know, uh, continue increasing people and, uh, and, um, you know, uh, uh, uniformity and yield and so on. So there's a lot of nothing to be done, but, um, nonetheless, we're very pleased that we have four layer full size cells working this early in the year, uh, because that gives us confidence that, um, that we, um, you know, uh, can, you know, we have a real shot of hitting the 8 to 10 layer cell by year end. And if we hit that goal, that would give us significant confidence that we can make a multi-layer full commercially relevant four-factor prototype to deliver to our OEMs to test. in 2022, and at that point, the risk drops even more. And then while I'm talking about this, I will say that the other key milestone is in 2023, we'll have a higher volume of cells, 200,000 cells a year, rolling off of our 2S0 pre-pilot line. That will be yet another important risk reduction step because that's the point at which those cells will go into your cars on test tracks. So these three or four milestones, the four-layer full-size cell, the eight to 10-layer full-size cell by year end, the multi-dozen-layer full-size cell by sometime in 22, and then the hundreds of thousands of full-size dozens of layers worth of cells in 23 that will go into real cars Every one of those, you know, handful of milestones represents sort of a step function drop in risk that we feel is going to, you know, really make the story that much more exciting. So we're careful to, you know, communicate both the results here and also the upcoming milestones. But every time we hit one of these milestones, as we have today, you know, I think we feel, you know, increasingly confident that we remain on track towards our long-term goals. And that's really all we can do is focus on execution. We believe that if we can execute, the value proposition is so compelling and the customer interest is so strong that we're going to end up really making a significant impact on the industry.
And there are no further questions at this time. Do you have any closing remarks?
I just want to thank everybody for making time to join us today. I think that, as you heard on the call, we're pleased with the results that we've hit so far in terms of the foreign air cell that I just spoke about, the zero pressure cell, the customer interest that we continue to see, the momentum that we have with our manufacturing line, we've secured the QS0 facility that will start to be turned up later on this year. And again, we're going to keep focusing on execution. And we believe that if we keep executing, that we will achieve our goals of really making an impact in this industry, helping to make a dent on emissions, and, of course, creating a lot of value for our investors. With that, I want to thank you all for joining, and we'll talk to you next quarter.
That does conclude today's conference. Thank you for participating. You may now disconnect.