This conference call transcript was computer generated and almost certianly contains errors. This transcript is provided for information purposes only.EarningsCall, LLC makes no representation about the accuracy of the aforementioned transcript, and you are cautioned not to place undue reliance on the information provided by the transcript.
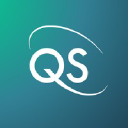
QuantumScape Corporation
4/26/2022
Good day and welcome to QuantumScape's second quarter 2021 earnings conference call. John Sager, QuantumScape's head of investor relations. You may begin your conference.
Thank you, operator. Good afternoon and thank you to everyone for joining QuantumScape's first quarter 2022 earnings call. To supplement today's discussion, please go to our IR website at ir.quantumscape.com to view our shareholder letter. Before we begin, I want to call your attention to the safe harbor provision for forward-looking statements that is posted on our website and as part of our quarterly update. Forward-looking statements generally relate to future events, future technology progress, or future financial or operating performance. Our expectations and beliefs regarding these matters may not materialize. Actual results and financial periods are subject to risks and uncertainties that could cause actual results to differ materially from those projected. There are risk factors that may cause actual results that differ materially from the content of our forward-looking statement for the reasons that we cite in our Form 10-K and other SEC filings, including uncertainties posed by the difficulty in predicting future outcomes. Joining us today will be QuantumScape's co-founder, CEO, and chairman, Jagdeep Singh, and our CFO, Kevin Hetrick. Jagdeep will provide a strategic update on the business, and then Kevin will cover the financial results and our outlook in more detail. With that, I'd like to turn the call over to Jagdeep.
Thank you, John. At the end of 2020, we unveiled single layer cell data showing a solid state lithium metal chemistry we believe is capable of delivering compelling performance benefits over conventional battery chemistries on key metrics such as energy density or range and charging time. Since then, we have not only shown further advancement of this platform, including repeated 15 minute fast charge and operation with zero applied pressure, but have also demonstrated that we can scale up to multi-layer cells using single-layer organ blocks. We continued the steady progress into 2022 by showing our very first 16-layer cell on our February earnings call and are pleased to note that we have now demonstrated results over 500 cycles with 16 layers under our gold standard test conditions with energy retention and cycling behavior similar to our single, four, and 10-layer cells. In addition, one of our key goals for 2022 is to demonstrate our proprietary cell format, which is designed to be flexible enough to unlock the benefits of our anode-free cell architecture while accommodating the uniaxial volume expansion characteristic of lithium metal anodes. This 16-layer result is in this proprietary cell format. We believe these results represent an encouraging proof of concept, and we look forward to sharing additional details on our proprietary cell format in the future. While we are pleased to share these results, we note that more work remains to be done on the quality and consistency of our materials and processes before we can achieve our goals of commercializing our technology. This requires a continued focus on improving our production tools and processes, as well as incorporating improvements in product design. We have encountered and expect to continue to encounter and work through a range of technical, engineering, and production challenges as we execute on our plan. However, we believe successfully addressing these challenges further strengthens the moat we have built around our technology with our IP portfolio, which now consists of over 300 patents and patent applications. In parallel with building up the layer counts of ourselves, we have also been working to increase the scale of our operations, One key constraint on this front has been separator production, and a key goal for 2022 is to ramp up the production of separator films with peak weekly starts of over 8,000. We're therefore happy to report that we recorded average weekly starts of over 3,700 exiting Q1 2022 compared to less than 2,000 exiting Q4 2021. This increase was made possible by new higher-throughput continuous-flow separator production tooling on our Phase I engineering line. The new tooling has also increased our confidence in a core component of our scale-up thesis, that larger-scale continuous-flow equipment can not only improve the throughput of our manufacturing process, but also deliver improvements in quality and consistency due to better process control. Increased throughput and better quality not only allows us to build more cells to test but also allows us to allocate a significant fraction of our separator films to perform other critical tasks, such as testing to automation and iterating on our manufacturing process. Over the coming quarters, we expect to take delivery and complete the qualification of many more large-scale and continuous-flow tools across our Phase I and II engineering lines and our QX0 pre-pilot lines. We continue to target delivery of A-sample cells to at least one customer in 2022. The A-sample is planned to have dozens of layers and is intended to demonstrate the core functionality of the battery cells. Automotive customers today are generally forced to make a choice between cells that offer higher energy but lower power or higher power but lower energy. We believe that in order to substantially improve both power and energy simultaneously, new battery chemistries are required. The core value proposition of our solid state lithium metal technology is the potential to shift the performance frontier on both energy and charging speed simultaneously. In that vein, in Q1, we announced a new deal with a third top 10 automotive OEM by Global Revenue. Upon achieving certain milestones, the deal reserves five megawatt hours of capacity for this OEM from QS0. our pre-pilot production line. The agreement also provides a pathway to establishing a US-based joint venture facility with up to 50 gigawatt hours in annual cell production capacity, subject to technical milestones and mutual agreement. This latest announcement is the fifth customer sampling agreement we have announced and affirms the strong interest leading automotive players have in adopting next generation battery technology. Lastly, a word on our strategic vision. Battery development and manufacturing is a complex undertaking that requires grit, determination, and disciplined execution. Since entering the public markets in 2020, our team has been focused on laying the foundation for what we expect will be substantial growth in our manufacturing and operational capabilities. 2022 represents an inflection point in this process and we believe we have shown that our long-term execution strategy is beginning to yield results. While substantial work remains to accomplish our 2022 goals, we believe this quarter's increases in film starts, progress on our proprietary materials and cell format, and manufacturing quality improvements represent a strong start towards achieving these milestones. We look forward to reporting continued advances on these fronts in the coming quarters.
With that, I'll turn it over to Kevin. Thank you, Jagdeep. In the first quarter, our operating expenses were $91 million. Our GAAP net loss for the quarter was $90 million. This level of spend was in line with our expectations entering the quarter. Cash operating expenses, defined as operating expenses less stock-based compensation and depreciation, were $57 million for the quarter. For full year 2022, we continue to expect cash operating expenses to be in the range of $225 million to $275 million as we focus on eight-sample prototype cell development and scale-up of our engineering line. We're trending towards the higher end of our cash OpEx guidance range as we are seeing signs of inflationary pressures, particularly on labor costs. CapEx in the first quarter was approximately $39 million, within our guidance range of $30 million to $60 million. Approximately 60% of our Q1 CapEx went towards our Phase II engineering line. The remainder of Q1 CapEx was primarily dedicated to progress payments on QS0 tools and initial facility spend on our QS campus build out. You can read about the details of our spend in the shareholder letter. We continue to expect total 2022 CapEx to be in the range of $325 million to $375 million and forecast second quarter CapEx to be in the range of $35 million to $65 million. For the remainder of 2022, We expect QS0 equipment and the continued build out of our expanded QS0 campus to drive the majority of CAPEX. We expect CAPEX investment during 2022 to be more heavily weighted towards the back half of the year. We continue to target that by the end of 2022, our engineering line will have achieved its goal of producing a sample prototype cells and that we will have received most equipment for QS0 towards our 2023 goal of producing candidate B sample cells from that line. In line with previous guidance, we forecast OPEX to grow steadily during 2022 and 2023 OPEX to grow modestly from 2022 levels as we slow our headcount growth rate, reallocate resources from development to manufacturing, and realize gains from investments into automation. Payments in 2021 and 2022 continue to represent the substantial majority of investment into our engineering and QS0 lines. Consequently, in 2023, we continue to forecast capital spending related to our engineering and QS0 lines to decline significantly. With respect to cash, we spent $87 million on operations and CapEx in the first quarter. We continue to expect to enter 2023 with over $800 million in liquidity. in line with previous guidance. We're excited to be underway on our goals for 2022, including the production and delivery of A-sample prototype cells and receipt of most QS0 equipment toward the production of B-sample candidate cells the next year. With that, I pass it over to you, John.
Thanks, Kevin. We'll begin today's Q&A portion with a few questions we've received from investors over the Say app and in our IR inbox. Our first question comes from the Say app. Solid-state batteries have recently become an auto industry buzzword, with nearly every automaker claiming they will be placing one in a vehicle in the near future. Can you speak to why QuantumScape will come out on top in this crowded house? What solid-state producers are the greatest threats to QuantumScape?
Sure, John. So, first of all, we see the level of interest in solid-state batteries as evidence of the need for disruptive new chemistry to improve battery performance on the key metrics, such as energy density or range and charging times. However, solid state by itself doesn't automatically mean better performance. The key is to show that your cells can deliver step change improvement over lithium ion batteries on metrics drivers care about, such as the ones I just mentioned. The hard part is meeting all the key requirements simultaneously, what we refer to as the AND problem. And the simple fact remains that we have yet to see anyone else, liquid or solid of any size, show data demonstrating cells are capable of delivering step change improvements to energy and power while also achieving 800 cycles on what we consider to be gold standard testing conditions including room temperature or 25 degrees celsius one hour of faster charging time and especially modest pressure so having shown data demonstrating our technology can do this we're now focused on scaling up along two axes greater layer counts and higher scale manufacturing candidly We believe that talking about scaling up before showing this basic capability is putting the cart before the horse.
Okay, great. Our second question is a short one. What is the current top priority for QuantumScape?
I would say there are three top priorities. So first, we need to scale our multi-layer cells up to higher layer count. Second, we need to scale our production capabilities up to higher film and cell count. And finally, we need to incorporate the new capabilities that we've already shown in single-layer cells, such as repeated 15-minute charge, into multi-layer cells. Now, achieving all these priorities requires continuing to deploy higher throughput and higher quality tools and processes, staying deeply engaged with our key customers, and continuing to recruit world-class team members. In fact, we have hundreds of positions open, and we welcome talented applicants who are interested in positively impacting the world.
Okay. Our final question from the CEAP, how do you plan on navigating the fact that lithium batteries are a finite resource and with time will become a more volatile good? Do you hope to create a quote unquote less is more model where you can get by on less actual lithium mass per battery?
So I think it's important to note that unlike combustion engines in which gasoline is burned irreversibly and turned into CO2 and H2O, with lithium batteries, the lithium is not consumed. It's simply shuttled back and forth between anode and kappa during charge and discharge. And when the battery reaches end of life, that lithium is still there and can be recycled. The second point I'd make is that unlike many other lithium metal solutions, which require lithium foils or other forms of excess lithium on the anode, we have an anode-free design, which means we use zero excess lithium. The only lithium in the anode is the lithium that's cycling back and forth between anode and kappa. In addition, it turns out there's actually a lot of lithium in the Earth's crust. Our CTO, Tim Holm, once estimated there's enough lithium for 100 million cars per year for a billion years. And finally, while we're talking about less is more, I should point out that our anode-free approach also uses zero carbon on the anode, so we eliminate the need for one of the most polluting steps of the battery supply chain. So to net it out, we believe this is fundamentally different from fossil fuel-based solutions. Of course, we as an industry need to continue to find the most sustainable ways to extract the lithium we do use.
All right, two more questions we received. Why the change in film size last quarter from 70 by 85 to 60 by 75? Does Phonscape need smaller film sizes to accommodate an increasing number of layers or for some other performance requirements?
So in the short run, our film size is driven by a balance between a number of key requirements. There's customer requirements, quality throughput, production equipment lead times. In the longer run, we can adjust our tool sizes, which enables us to make higher area films if that's what meets our customer needs.
Okay, thanks. What remains to be done on the proprietary cell format before that goal for the year is considered accomplished?
So it's mainly just making enough of them to give us further confidence in the design. We'd like to see a lot of data, gather a lot of statistics before checking the box on things like this. And this also gives us an opportunity to iterate on the design. And of course, any new design does require multiple iterations to work out all the bugs.
All right. And our final question is for Kevin. Kevin, you've talked about commercialization in the 24-25 timeline. Can you better define what you mean by commercialization?
Thank you for the question, John. Commercialization we define as the production of C-sample cells made available for sale to a third party. And we're currently targeting C-sample production out of QS0.
Okay, thanks so much, guys. We're now ready to begin the Q&A portion of today's call. Operator, please open the line for questions.
Thank you. If you would like to ask a question, please press star followed by one on your telephone keypad. If for any reason you would like to remove that question, please press star followed by two. Again, to ask a question, press star one. If you're streaming today's call, please dial in and enter star one. As a reminder, if you're using a speakerphone, Please remember to pick up your handset before asking your question. We will pause here briefly if questions are registered. The first question is from the line of Gabe Dodd with Cowan. Your line is open.
Hey, afternoon, guys. Thanks for all the remarks, and thanks for taking my questions. Kevin, I was hoping maybe we could just actually start with that last question from John just on commercialization and how that's defined. So C samples by 2425, is that correct? Is that a little bit of a shift in timing from when you guys had previously noted, or is that consistent with what you had been previously messaging?
Well, we think it's pretty consistent with what we've said before. Gabe, this is Jackie, by the way. I jumped in here. I'd like Kevin to jump in as well. You know, we believe we can, you know, take QA0 and actually get not just B samples out of there, but also C samples. And C samples, of course, are defined as cells that not only meet the commercial requirement, but also are produced on the tooling that will be used for production. So if we can actually expand QS0 to be able to produce cells for early commercial deployment, that would allow us to do that. And of course, the other part of QS0 is it's So, it's really the testing ground for all of our detailed processes and tooling and really the blueprint for manufacturing. So, we really need to get QA0 up and running because that will be the basis for expanding into higher throughput manufacturing plants by mid-decade.
Got it. Thanks, Jadiv. You hit on this a little bit again with one of the questions from John and also in the repair remarks, but just this proprietary cell format, also understand maybe not quite ready to share a ton of detail around it, but just curious if you could talk about how it has been performing relative to expectations and just accommodating volume expansion, and then how does this proprietary format change, if at all, the packaging step of the manufacturing process?
Yes, so the new packaging is a pretty key part of our overall cell design. As you point out, when you have a lithium metal cell like we have, especially an anode-free lithium metal cell, you have to be able to engineer a package that deals with that uniaxial expansion. The good news is the expansion is uniaxial, which means it only expands along one dimension. We can call it the Z dimension. It's easier to manage that than if we're expanding in three dimensions, for example, you know, if you have things like silicon in the anode, that expands in three dimensions as it soaks up lithium, and that's harder, we believe it's harder to manage. But, so we do have this design that is designed to manage that expansion. And in fact, as we mentioned in the letter, the cell that we reported that has achieved over 500 cycles was implemented in that design. So we feel that design has demonstrated that it has, a certain level of entitlement, so to speak. But it's not done yet in the sense that we need to do multiple iterations. We need to keep working out what I call bugs in the design as we iterate. And we're not ready to declare that we have checked the box on that. It's a goal for the year. But we feel encouraged that we've demonstrated that there's a basic level of entitlement there in that package that can get to 100 cycles with that design.
Okay, got it. Thanks, Jagdeep. I'll hop back in. Sure, Dave.
Thank you, Mr. Dole. The next question is from the line of Serini Pajuri with SMBC. Your line is open.
Thank you, and congrats on the progress, guys. Jagdeep, just going back to the previous question, On the 16-layer, I think you said it's greater than 500 cycles is the performance. And if you look at the history, you've been kind of consistently at 800 cycles at four layers and 10 layers and one layer. So is there more room to improve here on the 16-layer? And when should we expect that to hit? If it's going to hit 800, when do you see that happening?
Yeah, that's a good question. So, you know, if you look back at our history, you know, when we make first cells, we're happy to get any cycles at all. We keep improving the design. We get hundreds of cycles, and then eventually we get to fully mature designs that deliver on what we call the gold standard testing conditions, which includes hitting 800 cycles at 25 degrees Celsius, so basically room temperature, with one-hour charge and discharge power levels and under modest pressure, so not excessive pressure. And those conditions have to be met simultaneously. So what we reported is these cells, it's kind of a snapshot in time, over 500 cycles. We hope to report additional data over the coming year with these and other cells that can get to our target of 800 cycles. But also importantly, we've said in the past on a previous call that Our goal for the year actually is to have an A sample, and the A sample is going to be even more than 16 layers. So we are currently targeting dozens of layers that we believe will be capable of achieving our goal standard test conditions. So it's an aggressive goal, and that's really what we're targeting for this year.
Okay, thanks for that. And then one technology question. I think one of the benefits of solid-state, and especially you were product that you're targeting is fast charging, less than 15 minutes of time. Interestingly, if you kind of look at some of the recent announcements, for example, Kia and Hyundai, they're talking about the new EV6 charging in 18 minutes from 20% to 80%. I mean, I don't have one. I haven't tested it, so I don't know how legit those claims are, but just trying to understand Given that the traditional battery seems to be improving when it comes to fast charging, when you go into production, how much of an advantage do you think you'll have? And then less than 15 could mean less than it could be 14 or even 10. So where do you see that going longer term in terms of fast charging for you?
This is a great question, and I'm glad you asked it. If you look at our shareholder letter, we actually have a graph that addresses this exact question. It's called Shifting the Power Energy Performance Frontier. The key point is you can, in fact, make a battery today that can charge relatively quickly. The problem is if you do that, you have to trade off the energy density of the battery. So you can take a conventional chemistry and either optimize it for energy, meaning high energy but lower power, or optimize it for power, meaning higher power but lower energy. So in that graph, I think it's on page 7 of our shareholder letter, the first curve, the lower curve on that graph shows you what we believe today's chemistries are capable of. In fact, there are two data points on that curve that are from actual vehicles that are on the market today. One is a top-selling long-range EV, and the other is a leading high-performance EV. And you see that they're relatively similar chemistries, but they have different operating points on the power-energy trade-off. So the real question to ask when you hear someone saying 18-minute charge is, okay, 18-minute charge, but with what type of cell? Is it an energy cell or a power cell? So in this particular example that we show in our letter, the high-performance EV has a power cell, so it can charge on the order of, I think, 20, 22 minutes, but it has only about 600 watt-hours per liter at the cell level. And conversely, the top-selling long-range EV takes longer, about 35 minutes to charge to 80%, but has north of 700 watt-hours per liter. So the beauty of what we're doing is by changing the chemistry, you can kind of push the whole power energy frontier curve out and to the right. So if you look at the curve on the top, there you see that you can still have multiple operating points with the quantum scape chemistry. You can make a quantum scape energy cell or a quantum scape power cell. But in both cases, you have higher energy and higher power than what's available today. And we believe what is achievable with conventional lithium ion chemistry. So that's really the key point is you have to ask, You have to ask what the full package looks like. What's the energy? What's the power? What's the cycle life? Look at all those parameters together. Again, this comes back to the end problem.
One minor point to add to that from a vehicle perspective, power, of course, is charge time, and energy is, of course, range.
Right. Got it. Thank you. And then one longer-term question. This will be my last question, Jack, if I promise. So, you know, you talked about, you know, signing or at least interest from a third top 10 customer and potentially, you know, saying that that could lead to a JV down the road, you know, up to 50 gigawatts of capacity. I know it's early days and you have to meet a lot of milestones before we get there. But is that, you know, should that something we expect in the next five years or is it, you know, beyond the next five-year plan? Thank you.
I mean, no, it's something that we will work with these guys on, and as soon as we can reach agreement and as soon as we can start deploying, we will start deploying. As I said earlier, the precursor to any larger factories is we have to get QS0 done and sort of defined, because that will produce the blueprints that we're going to use for any factory expansion. The good news is that once we get QS0 producing real cells, we should be able to jump to higher capacity lines and be more efficient about scale-up. But this is a value point of this particular JV out because there really is an opportunity here to build a compelling US baseline with a really high level of capacity. 50 gigawatt hours is a big number. In fact, I believe 50 gigawatt hours is still larger than the largest currently operating battery factory. So it's a, you know, it's a real, it's a real, you know, factory.
Got it. Thank you. Absolutely.
Thank you, Mr. Paturi. The next question is from the line of George Giannarchis with Bayer. Your line is open.
Hey, guys. Good afternoon. Thanks for taking my question. First, maybe if you could talk about your long-term approach, again, that you're getting closer to building things around materials procurement and what sort of agreements you have out there, please.
Yeah, I'll take that. This is Jaydeep. You know, I guess the good news, in a way, is that we're still not shipping product commercially. So the volumes that we're currently consuming of materials is relatively modest. So we don't have any immediate issues relative to material supply. That gives us time to work with some of the leading materials providers. And our procurement supply chain teams are working with those suppliers to put in place agreements, which we believe can address the needs that we have. We also have this partnership with Volkswagen, as you know. Volkswagen is obviously one of the, you know, largest players in the automotive sector with a lot of, you know, a lot of sort of clout. And we think that partnership could be helpful relative to getting the attention of the suppliers as well. And finally, I'll say that, you know, a lot of the suppliers that we're working with sort of share our sentiment that the future of batteries and EVs is likely to be solid state. And if that's the case, then they want to be a part of that future. People want to go where the puck is going, so to speak. And so we've seen a relatively warm reception on the part of the suppliers that we work with. And obviously, we need to get these agreements finalized and turned into actual congressional commitments. But so far, we feel like we're engaged with the right players and putting in place the right kind of partnerships.
Thanks. And one more just around software. Longer term, what kind of role do you see software analytics playing in the offering that you'll give to OEMs for time? I'm sure you know that one of your competitors talks about a software package as an adjunct. Is that something you've considered as well?
Well, it depends on what kind of software you're talking about. We do a lot of use of software and machine learning models and things like that on the manufacturing side. It can be a very effective tool relative to screening films and identifying whether parts you're making are likely to be reliable or not reliable and so on. So we have some very strong partnerships with some key suppliers there. In fact, some leading deep learning model suppliers that are playing an increasing role in our metrology and manufacturing processes. However, if you're referring to players that are trying to use AI or machine learning models in the cell, in production, to try to detect a dendrite that's being formed in formation, to be candid, our belief is that if your system is already prone to forming dendrites, It's too late. It's just too late. You cannot try to identify dendrite formation using software and then try to somehow change your charge protocol or discharge protocol to slow down or stop the growth of those dendrites. We've had a lot of experience with lithium metal over the years and with dendrites. We can tell you that if your material doesn't fundamentally uh prevent end rights if there's a defect or a flaw of any type um you know it's uh lithium metal is going to win then rights are going to win so we don't think that's a viable strategy i don't think any automaker that we know of is going to accept uh the risk of a battery that could end right in the middle of operation and rely on on some predictive models to to prevent it from failing so again not sure what you're referring to but but the the key um the key point i'll the key I guess the distinction I'll draw is there's a tremendously high value relative to deploying software, machine learning models, you know, AI models on the manufacturing and production side. There isn't really, in our view, a viable way to use those models in operando to try to prevent dendrites.
Well, you guessed correctly. Thanks, guys. I'll go back and keep going. Thank you.
Thank you, Mr. GNR, Rick. The next question is from the line of Winnie Donald with Deutsche Bank. Your line is open.
Hi, thanks for taking my questions. I was wondering if you can talk about sort of like the line of visibility you have to taking, you know, the large scale equipment you've mentioned, the shareholder letter. And then if you can just walk us through how that would take you to, you know, 8,000 weekly film stars by the end of the year. And would you say that you're ahead of that goal so far since we're and you're already almost halfway there. Thanks. And I have a follow-up.
I would say that for the Phase II engineering line that's set to come up this year to produce the A sample candidate cells, there we have excellent visibility as that tooling is primarily on order at this point. And then I would say we have good visibility into QS0. We've provided it as a goal to land the majority of equipment this year towards start up of that line next year producing B sample candidate cells. So that was the visibility part of the question. Winnie, can you remind me if there was a second part?
Yeah, I'll take a second. I'll take a second.
Oh, the film start.
Go ahead. Yeah, on the film starts, we are actually pretty pleased with the 3,700 starts weekly average that we reported for the simple reason that we've been film constrained for quite some time now. We've known for, I don't know, over a year that we need to make more films because everything depends on our film quantities, not only making new cells to test and deliver to customers, but also things like qualifying new process equipment. When we make a new tool that has higher automation, our tool vendor, our tool partner, needs films from us to be able to develop and validate those tools. So there's an insatiable demand for supply of films or separators for all of our different development and manufacturing activities. And of course, the tough part is that to increase capacity or increase throughput of films, you need new tools, and those tools have long lead times. So increasing capacity tends to be relatively non-linear, more like a step function increase. And so the fact that we've gone from less than 2,000 films in Q4 to about 3,700 this quarter or in Q1, is a great sign that those new tools are not only in, but they've been qualified and they're operational. And in fact, as we point out in the shareholder letter, one of the key parts of our thesis has been that when we deploy those bigger continuous core tools, we not only would get more throughput, but we could get higher quality. And that's exactly what's borne out. So there's some graphs in the shareholder letter that Might seem technical a little bit. I think it's on page four. But to make a really important point, which is that if you look at a few of the key metrics we use for quality on the films, we're seeing better performance on those key metrics out of these new, larger, continuous flow tools that we have for the separator. So it's kind of a double win. We're not only getting greater throughput, but we're getting better quality films out. And of course, those two things are really the key to everything we do. So yeah, we're pretty pleased by that. And the goal for the end of the year was 8,000 films. We believe we're tracking to that goal. And if we can get there, then that means we should be in good shape relative to the rest of the goals we have this year, including the A sample.
Thanks for that. And then another one from me. I guess what's after 16 layers? Like, is there a... Is there more metal ground you have to cover before you jump to sort of, quote unquote, several dozen layers, for instance, 24 or 26, before you jump to several dozen things? I'm just trying to understand.
Yeah, I mean, obviously, our development teams are going to be assembling cells that have high and higher layer counts. I think the dozens of layers is just probably the most meaningful milestone because that's the point at which we believe there will be, in some ways, any doubts about whether the technology can be scaled up in terms of layer count will be put to bed. I think what we've shown so far is super encouraging. We went from single layers to four layers to 16 layers. But I think probably the most important part of of that multimeter scale that we've shown so far isn't just that we can scale these up and have the cells work, but that the cycling performance and capacity retention of those different cells is very similar. So if you look at the curve that we show on, I think on page three of the show letter, it's really hard to even tell which cells are which because the performance is so similar. This is important because if you remember, When we first announced our results back in 2020, some of the questions we got were around, well, what happens when you make multi-layer cells? Does this capacity, does this performance degrade? And what we've shown so far is no. When you build these cells correctly, you can get very similar performance on one, four, 10, 16 layer cells. And fundamentally believe that as we scale up to dozens of layers, we should be able to retain similar performance. And, you know, at some point, you know, having more intermediate milestones doesn't really add that much value. It's just about do we have an A sample that customers are excited about or not, and we've committed to trying to achieve that this year. So I think, you know, that will be a fairly important milestone for us. It won't be easy. But if we can get there, I think it'll be quite transformational.
Thanks for taking my question.
Absolutely.
Thank you, Ms. Stone. The next question is from Chris Snyder with UBS. Your line is open.
Thank you. And I actually wanted to follow up on those comments just made around the scaling up of the multilayer cell design. It seems like the company has been adding about six layers at a time, at least based on the test results in the shareholder letters that we've gotten. How does the company think about the magnitude of these increases? I assume the absolute level will increase. Is the percentage increased? the better way to think about it in that you know a year ago the company was doing four layers now we're doing 16 layers which is up 4x even though it's only 12 counts um you know just trying to get some more color around how the company thinks about that ramp as they as you work to deliver the a sample with dozens of layers by your end yeah i think the way we think about it is that you know we we make building blocks of unit cells and then we assemble the building blocks into bigger building blocks so
it's not like we add one layer at a time. So there is sort of more of a percentage effect as opposed to sort of a linear kind of effect. In fact, if you look at the slide on page two, it shows you kind of just a graphic of time on one axis and number of layers on the other. And you can see sort of almost an exponential-looking curve, right? And I don't mean to imply that we can extrapolate that curve all the way up, because there are no true exponential curves. You can't go to infinity, right? But it just gives you a sense that, you know, if you look at the time it took us to go from, you know, one layer to, you know, four layers, and then four to 16, you know, you're seeing, you know, relatively rapid progress. And again, one of the main constraints we've had is simply getting enough films, right? So the fact that we now have the film starts increased to 3,700 in this last quarter, that really was one of the key enablers If every time you make a cell you need 16 films, you need 16 times as much capacity as when you're making single-layer cells. So that's been one of the things we're happy to see progress on. But at the end of the day, we said publicly that our goal is to have a few dozen layers this year. Again, ambitious goal. We'll see if we can hit it. But if we do hit it, I think it's a very exciting milestone.
No, I appreciate that. Really helpful. And then for my second question, I wanted to talk about or ask about the scaling up of the separator film production and then specifically the charts on page four of the shareholder letter. You know, just to make sure I'm understanding them correctly. So when the company says it's averaging 3,700 weekly starts to exit Q1, does that translate to essentially production of of 3,700 separators, and of that 3,700 separator production, a bit over 1% of the output is meeting the company's assessment of good quality films, which is pretty significantly from the old process.
Where does the 1% come from? I'm sorry, I better answer the 1% number.
What's the reference there? Well, that's just where the blue line seems to be crossing over the green line. Oh, yeah, it's not 1%.
Yeah, I'm sorry. That line is 100%. So it's 1.0. The fraction is 1.0. So that black line in the top is 100%. So what these quality metrics are showing, so this is a good question. Thank you for asking because it's probably not clear what these graphs mean. But we wanted to share it because they make an important point. On the x-axis is a particular, a couple of different proprietary quality metrics we have that we, used to determine whether the films are good or bad. That vertical green bar, that shows you the reference level of performance or quality that we're looking for. If the quality metric is to the left of that line, that's a good film. If the quality metric is to the right of that line, it's a bad film. So what you see is the red curve, which is the previous process that we had, was producing films that were good I don't know, you know, on the left-hand metric, maybe looks like, you know, 30%, 40% of the time, and on the right-hand metric, maybe 60% of the time. With the blue lines, which is the new process using the new continuous core tools, we're seeing that you have a much higher fraction of forms, you know, well over 90%, over 95%, in fact. In fact, pushing 100% in the case of the right-most metric that, in fact, meet that performance threshold that we have. So that's what's exciting is that the number of films that are meeting the threshold is much higher. And of course, once you have those good films, you can use them for all the functions I mentioned earlier. You can use them to build cells to get the customers. You can use them to build cells to test different levels, different functionality. You can use them, you can drive them to production for tool and process development. So there's a lot of uses for films that we have. And what this chart is basically showing is that, you know, The number of the general quality of these films is higher than what we saw before. I want to be careful here. These are not the only quality metrics we use for the films. This is just a couple of the key ones. But on these particular metrics, performance has improved quite meaningfully, as you can see. And we still need to do work to improve quality on the films overall to get to our goals. But the main part we're making here is that the new tools with higher throughput also are producing, you know, better quality films, which is, you know, which is a win, right?
Oh, thank you for all that, Collin, and I appreciate you clarifying on the access. So thank you for that.
Absolutely.
Thank you, Mr. Snyder. The next question is from David Bell with Wolf Research. Your line is open.
Hey guys, congrats on the quarter. Thanks for taking my question. I wanted to follow up on the last point a little bit. Could you just clarify what has been the assessment from your team as to why these improvements are actually happening when you go to larger scale tooling and more continuous throughput?
Yeah, so basically the short answer is process control. These bigger tools come with better process control and To give you a sense, just to make it more specific, David, give you one specific example of how that works. These tools have different zones as the films are processed. Each zone applies a different profile. So you could have different environment, different temperature, different time as you process the film. And as the tool gets bigger, it actually allows you to have better isolation, for example, between zones, which means you don't have sort of a spillover of one set of conditions into the adjacent zone. So that's one very concrete example. But in general, the short answer is these tools are coming with better process control, which allows us to more tightly control the films and get better quality coming out of the films. And again, this has been a key part of our Our scale-up thesis is that higher throughput will likely produce better quality because you have more automation and less room for human error. But it's still, even though that was our thesis, it's just really great to see that thesis, you know, sort of playing out in terms of the actual quality of the film.
Thanks, Jagdeep. And just shifting directions really quickly to chemistry, can you comment on how your conversations with the auto OEMs have evolved over the last quarter? as issues with nickel have come up? Are they looking to change the direction that they want to go to leverage your battery technology?
Well, you know, I'll say a couple of things about that. One is, of course, as you know, our system is cathode agnostic, right, which means that we actually, you know, don't tie the automaker to nickel, right? If they choose, they can use a lithium-ion phosphate system, and we've shown that our system works with lithium-ion phosphate, right? The second key point I'll make is that in our system, because we don't have an anode, which means no anode materials costs and no anode processing costs, the overall system, we believe, ends up being more cost effective whatever your baseline, right? So if your overall, if the spot price of nickel goes up, then of course everybody pays more for cathodes. But that same material with an anode-less design is going to have lower active materials costs than one that also requires carbon or silicon or lithium metal or something else on the anode. And then in general, what I'll say is the separator as well is a material that, as we mentioned before, has established supply chains that already exist for all of its key precursors. So to summarize, we kind of feel like our system has some fundamental first principles and advantages relative to raw materials requirements, right? Our anode doesn't exist, our cathode is agnostic to specific materials, and our separator uses global commodities as precursors. So when you put it all together, I feel like it's not While it's not ideal for the industry to have all these supply constraints to deal with, this architecture is probably better suited to deal with these constraints than conventional architectures.
Thanks, Jack Deep. And just one more quick one from me. Could you give me a sense of how many pre-A sample cells you've actually delivered to OEMs and what size cell have they been? Has it been the 16-layer cells? And are the OEMs largely reporting the same sort of data that we're seeing here today?
So I don't know the actual numbers, so I can't give you any specific numbers there. I think the show notes there actually points out, if I'm not wrong, I can just quickly in real time scroll down there. I don't want to say anything that isn't publicly disclosed. But I think we actually point out that we've shipped multiple generations of cells to multiple customers across both automotive and other applications. And, in fact, we also say that in Q1, our 10-air cells, were successfully tested by one automotive customer and entered the testing phase with another. So that's what we said in the show. I'm going to stick with that. But I think we are, you know, certainly, you know, our process is to develop, you know, new capability in-house, then work through all of the, you know, what I call, you know, bugs or iterations as you go through the design and production of it. And finally, when we get to a level of reliability and confidence based on statistics and data, that's when we provide cells to customers. One quick thing about your previous question as well. I mentioned that we may have some advantages relative to supply chain in terms of not needing an anode, being cathode agnostic, and having a separator that uses global commodities as precursors. The one thing, of course, that we still need is lithium. Our cell is lithium metal, so the lithium that goes into the cathode So it has to be there. And on that front, even we also have an advantage, which is that our system, if you recall, is an anode-less design. So we don't need lithium foil. For example, there are some lithium metal approaches that use lithium foil. And so in our case, the only lithium on the anode is lithium cycling back and forth, which actually you can't have any less lithium in the cell than that. So we kind of feel like, again, it's not ideal for the industry to be in the supply crunch mode. But if you're going to operate in this kind of mode, having a system that's anode-less, that's carbon agnostic, that's no carbon, silicon, or lithium required on the anode, and has global commodity precursors for the separator, is probably the most robust system that you could have in these times.
Thanks, Jack Deep. Thanks for taking my questions. Absolutely.
Thank you, Mr. Bell. There are no additional questions waiting at this time. I'm now turning the conference over to Mr. Singh for any closing remarks.
Yes, so on a personal note, I'd like to say that with the exception of satisfying tax obligations and covering expenses related to the acquisition of QuantumScape stock through exercise of options I hold, I'm committed not to sell QuantumScape shares until we deliver a prototype sale to an automotive customer. And on that note, I'd like to thank everyone for joining and look forward to seeing everyone again next quarter.
That concludes the Quantum State Q1 2022 earnings call. Thank you for your participation. You may now disconnect your lines.