This conference call transcript was computer generated and almost certianly contains errors. This transcript is provided for information purposes only.EarningsCall, LLC makes no representation about the accuracy of the aforementioned transcript, and you are cautioned not to place undue reliance on the information provided by the transcript.
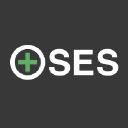
SES AI Corporation
3/14/2023
Hello, and welcome to the SES AI Corporation Fourth Quarter Earnings Call. My name is Alex, and I'll be coordinating the call today. If you'd like to ask a question at the end of the presentation, you can press star 1 on your telephone keypad. If you'd like to withdraw your question, you may press star 2. I'll now hand over to our host, Eric Goldstein, Vice President of Investor Relations. Please go ahead.
Thank you, Operator. Hello, everyone, and welcome to our conference call covering our fourth quarter 2022 results. and financial guidance for 2023. Joining me today are Qiqiao Hu, founder and chief executive officer, and Jing Nialis, chief financial officer. We issued our shareholder letter just after 7 a.m. today, which provides a business update as well as our financial results. You'll find a press release with a link to our shareholder letter and today's conference call webcast in the investor relations section of our website, at ses.ai. Before we get started, this is a reminder that discussion today may contain forward-looking information or forward-looking statements within the meaning of applicable securities legislation. These statements are based on our predictions and expectations as of today. Such statements involve certain risks, assumptions, and uncertainties which may cause our actual or future results and performance to be materially different from those expressed or implied in these statements. The risks and uncertainties that could cause our results to differ materially from our current expectations include but are not limited to those detailed in our latest earnings release and in our SEC filings. This afternoon, we will review our business as well as results for the quarter. With that, I'll pass it over to Chi-Chao.
Thanks, Eric. Good afternoon, everyone, and thanks for joining our fourth quarter conference call. As the leader in lithium metal batteries, SDS continues to evolve and innovate. Despite all the challenges that come with new battery development, we have made some exciting progress that we would like to share with you. 2022 was a difficult but productive year. We built and completed three A-sample lines, one in Shanghai, China, and two in Chungcheongbuk-do, South Korea, one for each of our three OEM JDA partners, GM, Hyundai, and Honda. The necessary level of dedicated engineering, quality, and production output required us to have dedicated lines for each OEM. Importantly, we achieved ready-to-use status for all three A-sample lines, under budget and ahead of time. This experience strongly supports our strategy of building lithium metal cells using lithium ion manufacturing process and building A and B samples in Asia so that we can come back to the U.S. for C samples and commercial production in the most efficient way possible. SDS was the first battery company in the world to introduce 100m power lithium metal cells. the first to enter an automotive A-sample JDA with a major OEM, and the first to encounter all the startup issues that come with producing 100-amp-hour lithium metal cells at pilot scale. As we detailed on our previous earnings call, we encountered countless issues ranging from ultra-thin lithium anode wrinkling and tearing during large-format rolling and lamination, novel electrolyte solvents go up electrical stacking misalignment and overhead powder formation during electrical punching formation pressure and voltage stability finding efficient ways to do image scanning on large format cells and developing proper ways to store handle tests and recycle lithium metal cells one really important thing we have learned over the past decade of development When our team can identify a specific issue, we are not that far from solving the problem. Over the past year, we have leveraged the deep lithium-ion stacked pulse cell engineering, manufacturing, and quality experience of our own team and our OEM partners and made a lot of progress. Identifying and solving these issues has provided great know-how and knowledge for our human engineers and scientists and a machine-learning-based algorithm, Avatar. By the end of 2022, Avatar could predict 100 mPower cell safety and life with more than 60% accuracy compared to 0% in the beginning of 2022. In comparison, Avatar could predict 4 mPower cell safety and life with 99% accuracy after three years of data training. Our three ASIMPLE lines provided a platform for us to work closely with each of our OEM partners and get hands-on live feedback. Our partners were stationed in our facilities for months at a time, and we attracted top engineering talent and worked with top vendors from around the world. It was accelerated learning for us in manufacturing and quality control. During the year, we also made significant investment in the province of Chungcheongbuk-do in South Korea. Our investment followed LG Energy Solution investment in the same province, making Chungcheongbuk-do the province with the highest battery production capacity in South Korea. During the fourth quarter of last year, I met with the president of South Korea, Seok-hyo Yoon, to thank him for supporting the industry and helping to build a robust supply chain around the world. I am extremely honored that we were recently awarded cash grants from the South Korean central government, represented by the Ministry of Trade, Industry, and Energy, Chungcheongbuk-do Province, and Chungju City, which will help us expand our capabilities in South Korea. The thing I am most proud of over the past year is how the entire SES team has worked as one. Our Boston team is developing new electrolytes and anode materials. Our Chongchun Bokchou team focuses on assembly equipment and cathode processes. And our Shanghai team focuses on electrolytes, annual manufacturing processes, and cell assembly processes. All of these contributions from our global team are being integrated into a system for our 100m power lithium metal cells. We recently summarized our latest large cell test data and published the results on our website. We believe this is the most complete data report on large-format lithium metal cells anywhere, and we will continue to publish similar data reports to keep the industry updated. We believe in transparency and are confident that a year from now when we publish additional reports on our large cells, the data will be even stronger as we continue to improve everything from materials to engineering to manufacturing quality. As the pioneer in lithium metal, We are also writing new protocols for the proper way to store, handle, and test lithium metal cells and interpret data. We are sharing this information with the battery community to help set new industry standards. To that end, we participated in the recent workshop on lithium metal batteries in San Diego. It was great to see so much excitement from academia, industry, national labs, and government agencies for the future of lithium metal batteries. We expect 2023 to be an exciting year for SCS. As we are upgrading our manufacturing lines, here are a few things we are working on internally and with our OEM partners. We're adding CT and X-ray imaging tools, custom-built for our large 100 MPa cells. We're adding new powder removal tools to remove all metal powders rising from the electrical counting process. We're developing entirely new anode processes from ingot to thick foils to thin foils and to the final anode to better control quality and performance. We're coating cathodes in-house to better control quality and experiment with new formulations. And we are scaling up novel solvent and salt production lines to better control quality and speed up the feedback cycle from designing new solvent molecules to getting data and making conclusions. Perhaps the most important thing for 2023 is that we are preparing for B-samples. This year, we plan to take our collective knowledge and experiences from our A-sample lines and we will design and build new B-sample lines. Our A-sample lines are semi-automated with a capacity of about 0.2 cells per minute or five minutes per cell. B-sample lines will be fully automated with about five cells per minute. Having the ability to produce more cells and generating more meaningful data on the far greater universe of experiments will further accelerate our human and machine learning, which will also allow Avatar's prediction accuracy for cell life and safety to increase quickly. Importantly, these new lives will also go a long way to proving the manufacturing feasibility and scalability of our practical approach to making liquid metal cells. As part of our preparation for B-samples, we plan to double our material R&D team, double our cell engineering team, double our manufacturing team, and nearly triple our quality team. This increase in our headcount is a natural evolution of our growth as a company and is reflected in our financial guidance for 2023. We will also hire a new chief manufacturing officer who has experience in running cell engineering, manufacturing, and quality management, and working with global OEMs to commercialize new battery technology. Compared to the major lithium-ion producers like CATL and LG Energy Solutions that have more than 3,000 quality checkpoints, we currently have about 200 quality checkpoints. Once we enter B-sample agreements with our OEM partners, We can no longer benchmark ourselves against other battery startups. We will be playing in the big leagues and will be held to the same standards that the OEMs currently use for commercial lithium-ion producers. With the dedication of our global team, the accelerated learning of Avatar, and the support of our OEM partners and vendors, we are confident that we will face the new challenges and overcome them as we continue to enter uncharted territories. SCS is profoundly American with its roots in the basement lab of MIT back in 2012. At the same time, SCS is also profoundly global with its talent and partners from around the world. As we prepare for B-samples and commercial production beyond that, we are preparing to expand back home in the U.S. This includes preparing for production capabilities for lithium metal cells, novel lithium salts and electrolytes, and lithium metal anodes. SCS plans to leverage experiences from global lithium ion players, new material innovations, new machine learning tools for safety and life prediction, and quality management, and the abundant natural resources in North America. In 2021, we were the world's first to enter automotive A samples for lithium metal. In 2022, we laid the groundwork for transitioning to B samples, In 2023, we will transition to B samples and lay the groundwork for C samples, commercial production beyond that, and building a robust next-generation EV battery supply chain here in North America. I will now turn the call over to Junie Ellis, our Chief Financial Officer, to review our fourth quarter results and outlook.
Thank you, Qichao. Good afternoon, everyone. Today, I will cover our fourth quarter financial results and discussed our operating and capital budgets for full year 2023. In the first quarter, our operating expenses were 20.7 million, an increase of 10.6 million from the same period last year. Stock-based compensation expense was 6.8 million a quarter. We reported R&D expenses of 8.3 million, an increase of 3.1 million from the same period last year. This increase reflects higher personnel costs due to increased headcount to support battery cell development, an increase in lab consumables and material supply, and the increase in development costs related to our advanced AI software and battery management systems. Our gross R&D spent in the first quarter was $13.5 million, which was offset by $5.2 million billed to our OEM partners. which are treated as counter R&D expenses. Our T&A expenses were 12.5 million, an increase of 7.5 million from the same period last year. Similar to the third quarter, this increase was primarily driven by higher personnel costs to support our operations as a public company, higher insurance costs, and the increase in professional fees and outside services. We incurred a non-cash gain of 9 million at the end of the quarter associated with a change in fair value of our sponsor earn-out liability. As we have previously outlined, certain tranches of our sponsor earn-out shares are accounted for as a derivative liability measured at fair value based on the price of our common stock at the end of the quarter. For full year 2022, cash used in operations was $46.5 million, and was less than our previously provided guidance of 55 million to 60 million. The lower level of spending reflects a combination of some conservatism on our part and lower overall spending for materials built south. Despite the lower level of spending, we were moving forward with our OEM partners and they're on track to transition to B samples this year. CapEx for the full year was 14.7 million and was below previously provided guidance of 20 to 25 million. Lower CapEx in 2022 was mainly due to payment timing. Looking at liquidity, our balance sheet remains very strong. We ended 2022 with a much higher than expected level of cash and short-term investments of 390 million, which we continue to believe is sufficient funding to get to commercialization. For 2023, we are providing the following financial guidance. We expect cash usage from operations to be in the range of 80 to 100 million and capital expenditures in the range of 50 to 70 million. We expect total cash usage for the year in the range of 130 to 170 million. This higher level of spending is necessary to support our growth as we expect to transition from A samples to B samples in 2023. Significant areas of spending in 2023 include the following. Headcount. We expect to double the size of our teams in material development, cell development, and system development, and triple the size of our quality teams in order to continue to improve our battery performance, establish a robust cell engineering design manufacturing platform, and significantly improve our safety prediction algorithm. Lab expansion. We plan to expand our US lab space to further strengthen our fundamental electrolyte and animal material development capabilities. Equipment and manufacturing facilities. We will work with our OEM partners to build highly automated production lines and highly efficient manufacturing facilities to support B sample development. We will also work closely with our OEM partners on quality and yield improvement initiatives and will upgrade our existing manufacturing lines by adding new tools as outlined by QCAL. Last, materials. We expect to spend more in this area as we anticipate manufacturing at higher volumes to meet our OEM partners' needs as well as our own development needs. 2023 is shaping up to be an exciting year of growth and investment for SES. We appreciate the support of our shareholders, employees, and OEM partners. With that, I will hand the call back to Eric.
Thanks, Jing. Alex, can you open the line for questions now?
Thank you. As a reminder, if you'd like to ask a question, you can press star 1 on your telephone keypad. If you'd like to withdraw your question, you may press star two. Please ensure you're unmuted locally when asking your question. Our first question for today comes from Winnie Dong of Deutsche Bank. Your line is now open. Please go ahead.
Hi. Thank you so much for taking my questions. First question is, could you give us a sense of maybe the type of feedback that you've been getting from your JDA partners from the assembly sales? And then again, for e-sample sales this year, perhaps maybe a sense of timeline for delivery. Is it still sort of like a mid-year target? Thanks.
Yeah, Winnie.
So we've been sending samples to our three JDA partners for testing really since the beginning that we entered into a sample back in 2021. And then just over the past two years or so, we made a lot of progress both in terms of the material performance as well as manufacturing feasibility. And the one key aspect of all three A-sample JDAs is basically to demonstrate the manufacturing feasibility of lithium metal cells. And the fact that we built three A-sample lines and then we delivered total production we both tested and delivered total about a thousand of these large lithium metal cells just last year. And then also improved the performance of these cells quite a lot. So that overall gave the OEMs confidence with both the performance that we demonstrated as well as the manufacturing feasibility. And then, so this is why we are preparing to enter the next phase. And then in terms of timing of the B sample, I mean, the B sample is really, it's not like a single point milestone. It's not like today you all of a sudden go from A sample to B sample. It's a process. And then for us, when or this B sample itself, it's not really about marketing for us. It's this gradual progress that will happen this year. Basically, continue to demonstrate the manufacturing feasibility at a much higher level, much better quality, much higher output. So it will happen around mid this year. And then whether when we're going to make announcements, that's another story that I really don't care about. But fundamentally, the company will enter into B sample and then it's a very core milestone. And then it's a validation both to the material improvements as well as the manufacturing feasibility that we have demonstrated.
Thanks so much. Okay, thank you so much. As you look ahead to sort of like 2023, I know you've, you know, talked about sort of like headcount expansion and, you know, equipment and manufacturing facilities and then continue to, you know, invest in materials and things like that. If you were to maybe like boil it down to a few sort of like key milestones to achieve by year end, you know, what can we look to as sort of like the scorecard by this year?
Yeah, a few things.
One is quality. And then last year, I would say that was the first year we started doing pilot scale manufacturing of these large cells. And the quality was actually pretty bad. And this is why we had a lot of issues that we addressed. And then this year, the quality basically needs to be at an entirely new level. And then also SCS as an organization, When we were in A sample, we still had sort of a startup organization. And now as we prepare for the next phase and then B sample and then project management, quality management, manufacturing, supply chain, all these managements will really enter into an entirely new level. And then we are putting systems in place to really make SCS as an organization a lot more capable at manufacturing and quality. So one key thing is not just band-aid improvements to improve the quality, but fundamentally improving the organization. So it's capable of a much higher level of quality and manufacturing management. I think this is probably the biggest milestone. And then at the same time, I mentioned earlier. So the A sample is about 0.2 CPM, so five minutes per cell. B sample roughly is about five cells per minute. So the speed at which we need to build these cells will be much, much higher while entering into a new level of quality. And then a couple other milestones including some of the new materials that we've been working on, new electrolytes, new anodes, and then the scaling up of these materials because we'll be making cells at much higher speed. That means all these new materials that we've developed, we'll also need to make these materials at much higher volume.
got it thank you so much um if i can squeeze one in this one this one's for jim um i guess on your cash using operation and class expand for 2024 uh you came in sort of like much lower can you just remind us what were the factors that contributed to like sort of the lower spending and could that also be you know some conservatism big into your 2023 numbers
So for 2022, the lower level of spending is part of that is just being conservative and be careful with our cash. And then the second part is really, as Chi-Cheung mentioned in the last earnings call, that we are focusing on building cells just to solve issues, not just to build cells for the sake of building them. So we build less cells in 2022. comparing to the original plan. So those are some of the drivers for 2022. For 2023, I think the, as I mentioned during the call, a lot of these fundings go into the growth part of our business. We have a pretty aggressive hiring plan and we're pulling forward some of the spending to build B-sample lines so that we can be ready to transition into B-sample this year with our OEM partners.
Great. Thank you so much for taking my questions. Thank you.
Thank you. Our next question comes from Gabe Daoud from TV Cohen. Gabe, your line is now open. Please go ahead.
Hey, everyone. Thanks for taking my questions and for all the detailed remarks so far. Chitra, I was hoping maybe just at a high level you could provide some of your thoughts around One of your OEM partners, GM, potentially shifting towards cylindrical cells versus pouch with Samsung has been kind of reported recently in the news. Just curious if you worry or you just think about maybe OEMs continuing to make a shift towards cylindrical as a way to optimize costs at the expense of high-performing anodes via pouch cells. Just any color on that would be helpful.
Yeah, I can comment on the particular choice of formats, especially for GN. I mean, one thing that we are working on with all the OEMs is basically trying to find the optimal form factor at the end. For example, is it going to be a 100 m power pouch cell? Is it going to be a 100 m power but in prismatic cells it's going to be a 70 amp hour, it's going to be a 60 amp hour, it's going to be a 50 amp hour. What is the final optimal basically cell design? That's actually part of this A sample and B sample work. And then we are testing, for example, 100 amp hours, 70 amp hours, 60 amp hours with, for example, high nickel cathodes, blend cathodes, different types of cathodes because the final cell, the final format is going to be based on a holistic consideration of safety, performance, cost, several factors. And the fact that we build 100-amp-hour stack pop cells doesn't mean that we will end up actually putting 100-amp-hour cells inside the car. It's more to understand the boundary of the The final cell, my variable B, a 70 m power cell. But all this, we build A samples and also B samples and then we improve the quality and then increase the production output so that we can collect more data and then also run more experiments faster so we can make all these, so we and our OEM JDA partners can make all these decisions based on data. And that's what we've been focusing on, stacked power cells, maybe stacked prismatic cells, and then also with different cathodes and also just the capacity of the cells. We'll also test a range of different capacities so we can find the optimal final cell design that we can actually put inside a vehicle based on a complete a very holistic consideration of lots of different factors. Got it.
Got it. Okay. Okay. That's helpful. And then, uh, you mentioned data. So maybe a good segue into a question on avatar, you know, to have some of the challenges that actually enabled you to, um, drive an improvement in, in tracking or predicting, uh, cell safety on the larger, uh, amp hour, uh, cells with 60% accuracy versus 0% in the beginning of the year. So, And then the smaller cells have 99% accuracy. So could you maybe just talk a little bit more about Avatar and the progression there and some of the improvements there that you're seeing?
Yeah, so we really found Avatar is a necessity. And then beginning of last year, beginning of 2022, because we didn't really have any large cell data, and Avatar is basically very data-driven. So we had zero capability to predict anything to the larger cells because we just didn't have any data to begin with. And then we collected more data. And then these larger cells are actually quite different from the smaller cells. For example, the impedance is much lower. And then any variation in impedance and a lot of the parameters that we use to predict health and life in smaller cells just simply don't work when we scale up to the larger cells. So we had to develop new parameters, and then also we also had to collect a wider spectrum of data. For example, the smaller cells with the current voltage and temperature, now we're doing current voltage, temperature, and pressure. Pressure is a really important factor in predicting health and safety of these large metal cells. And then also based on the data that we collect, we also both through a combination of internal physics based models where we actually predict health based on actual fundamental physics mechanism as well as just machine learning models that actually recommended very interesting parameters. So now with more data, So last year, 2022, we had A sample lines, and then we built and we tested about a thousand of these cells. And then based on that data pool, we got about 60% accuracy. Now that as we prepare to enter B sample with much better quality, much better consistency, and much higher output, then we expect the both the quality of the data as well as the size of the data pool to significant growth. And then that will significantly improve the accuracy of Avatar for the larger cells even faster.
Got it. Thanks, Chi-Chi. Thanks, everyone.
Thank you. Thank you. As a reminder, if you'd like to ask a question, you can press star 1 on your telephone keypad. Our next question comes from Sean Severson from Watertower. Sean, your line is now open. Please go ahead.
Great. Thank you. Good morning, everyone. I wanted to go back to the B samples this year and look at kind of what gives two things. What gives you the confidence that they'll be achieved this year? And then second to that, Has this economic environment, or what's called the volatility, have you sensed any changes in how OEMs are looking at things and timing, or they're just kind of plowing right through this because they have to?
Yeah, on the first one, well, so, I mean, A sample, B sample, these are not really magic, right? There's a formula behind it. It's a step-by-step, very clear process behind it. And so last year we were in A, and then we had a lot of quality issues and the volume was just not so high. So we've addressed and solved a lot of them. And then also to accelerate the learning. So lithium metal is a totally new thing. And then before the industry put lithium ion into cars, lithium-ion was using consumer electronics and laptops and other industries for a long time. So the automotive industry already had a lot of data and then a lot of experience with lithium-ion. Now, because lithium metal is totally new, and also we improved the quality and manufacturing feasibility to a level so that we were ready to take this to a new level so that we can actually manufacture more cells and then collect more data. One of the key reasons of doing A sample is, of doing B sample is A sample was still not fast enough. And just the amount of data and the amount of experience that we and our OEM JDA partners collected just was not fast enough. So we want to go to B sample so we can have this data and learning much faster. And this is why we are preparing to enter into B. We couldn't do that earlier because we still had some pretty key quality issues and then it didn't make sense to enter into B without solving these issues. But now we've solved a lot of the core quality issues and also we are putting systems and then also upgrading the organization So if it's time to enter into B, it will be accelerated learning completely A sample. So, yeah. This is what we and OEM partners are planning to enter into B. It's not magic. It's great. And then...
Nor is that economically sensitive or anything like that. This is just a natural progression that isn't going to be really delayed for any reason, I guess, because, like you said, it's all formulaic, right?
Correct. And, I mean, the economic environment so far hasn't really played a, I mean, hasn't really impacted the A sample, B sample decisions.
And in your conversations with OEMs, I know it's a bit of a guessing game, but when you look out, you know, when they're thinking like model year, you know, production for something like this, if you're in A and you're going to B this year, what does that translate into, into timing when in their minds they'd be thinking about production scales?
Yeah, I can't really go into details of that, but I mean, if you think about it, we're going to be this year, and then end of 24, C, and then, so we're talking about 25, 26, basically a new model vehicle being introduced.
Okay. Last question is on the supply chain. Obviously, lots of focus in the industry, domestic production and all the things we all know very well. And you've been focused on that for, you know, even before the Inflation Reduction Act and all of these things. Just wanted an update. Are you seeing that really come together? I mean, has there been a good push as you see it through your supply chain to meet those deliverables when the time comes, you know, for large-scale productions? Yeah, yeah.
Yes, I mentioned earlier, we're really targeting 2025-2026 for the larger scale introduction of lithium metal into vehicles. And then already right now in 2023, we and then a few suppliers were planning to implement capabilities for lithium salt, electrolytes, and then also lithium refining capabilities in Northern America. And then a lot of these implementations will take about two years. So by the time 2025 comes and then lithium metal is ready for commercial, several of the key materials, at least from our perspective, electrolyte and lithium anode, will also be sourced in North America. So we are preparing both the cell level as well as the material level in parallel.
Great. Thanks, Qiqiao. I'll jump back in the queue. Thank you, Qiqiao.
Thank you. We currently have no further questions for today, so I'll hand back to Qiqiao for any further remarks.
Yeah, so back in 2021, we were the first to enter automotive A sample. And then last year, 22, that's when we really started manufacturing lithium metal cells in pilot scale. It was really difficult because it was something no one had done before. And we encountered a lot of issues and we were very transparent on those issues, but we also made tremendous progress solving these. Now, entering B sample is, It's not a magic, it's just the natural next step. And it will be a huge milestone, not just for us, but the entire industry. It will be a huge validation for our practical approach to making lithium metal cells using lithium ion manufacturing process. It's something that we've been talking about since the beginning. And also, it will be a huge step forward for our OEM partners. So we made a lot of progress, but still a lot of work to do, and I hope everyone will stay tuned, and we will provide lots more exciting updates later. So thank you. Thank you for joining today's call.
You may now disconnect your lines.